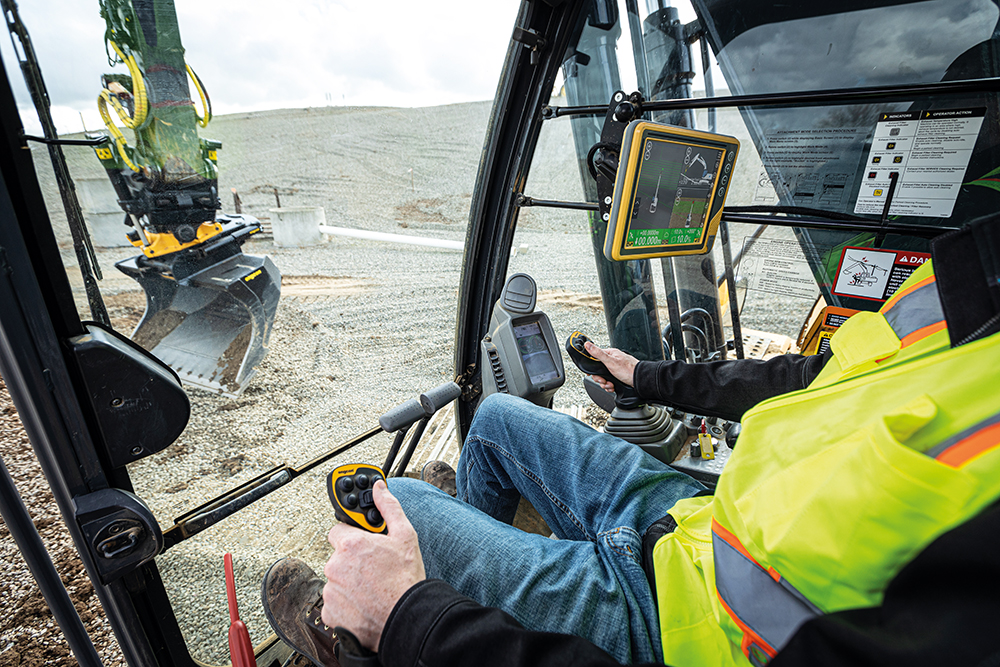
What are the benefits of automated, mastless machine control? Is it worth the extra investment? This CPD, in association with Topcon Positioning GB, explains.
Machine control (MC) is advancing all the time and it can be difficult to know which solution suits your site and your team the best.
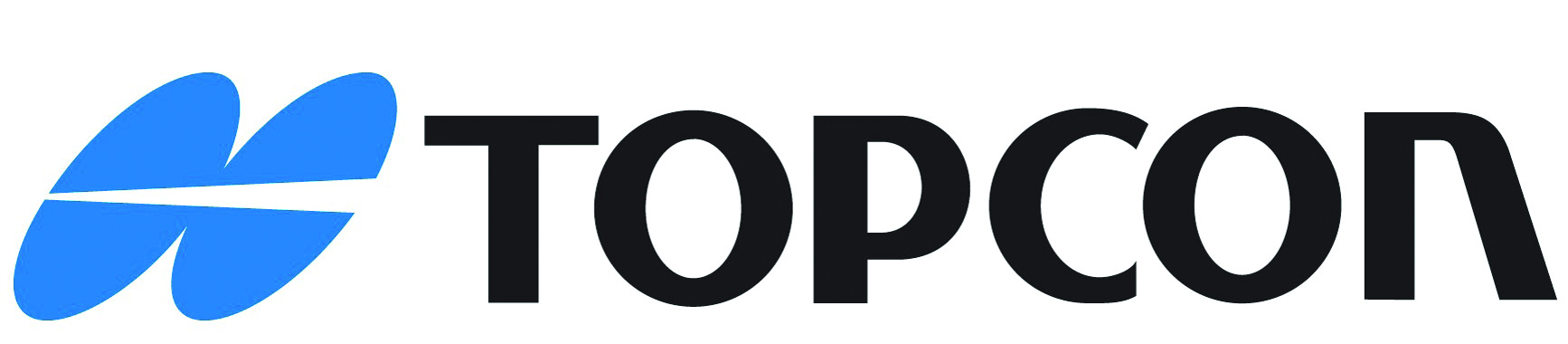
Automated MC solutions, such as Topcon’s MC-Max, help to increase processing power, speed, accuracy and reliability and can be installed on a full range of dozers and excavators, using the same basic modular components. But there are other reasons to invest in an automated machine control solution over older technologies.
A more efficient solution
The latest solutions are linked to cloud software, which means that data can be saved and updated in real-time, helping you to keep track of progress throughout the whole project.
This also means that machines can be controlled from remote locations. An operator could be in Portsmouth and control an excavator or dozer on a site in Aberdeen. This has made remote working possible for the construction industry for the first time, because you can trust your machine to do the job without needing to monitor progress on site.
While the software capabilities have advanced, the system functionalities stay the same, so you can jump in and use it straight away if you’ve used the same operating system on older kit. If you haven’t used software like Topcon’s before, these systems are simple to understand and full training is provided.
In terms of the physical benefits, newer technologies like the MC-Max offer flexible mounting solutions, as well as optional automatic blade and bucket control for a variety of machines.
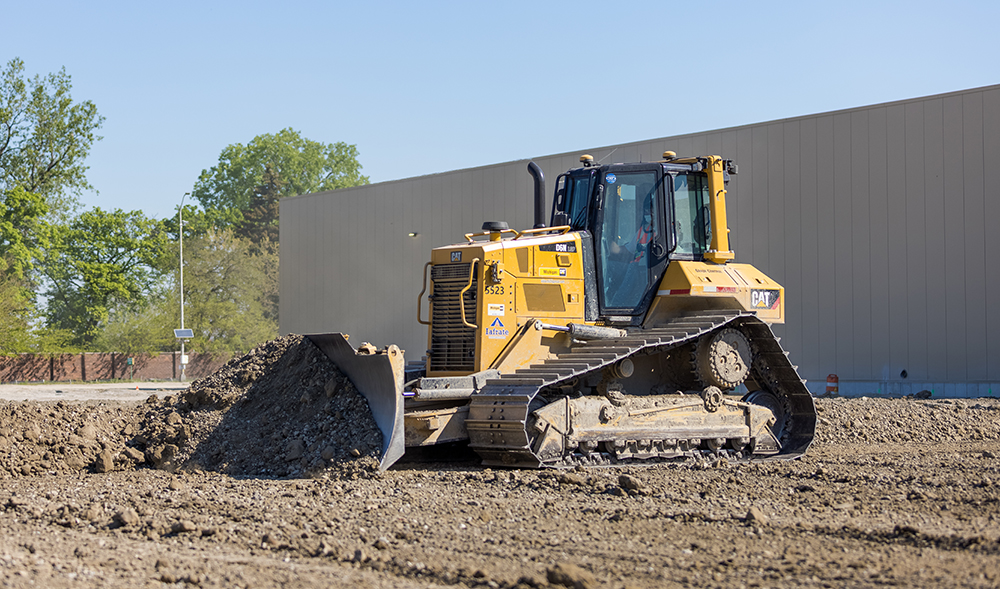
One of the most significant differences between older machine control solutions and the latest automated kit is the antennas and sensors. Topcon’s MC-Max solution uses two GPS antennas, mounted on the roof of the machine, which provide accuracy and positioning of the blade, working in conjunction with the hydraulics. Unlike older kit, like 2D or LPS systems, there are no masts or issues with getting the receivers off the blade, which offers improved visibility.
Topcon’s solutions in the MC-X family use TSi4 sensors: one to measure the pitch and roll on the body of the machine, three sensors to measure the C frame which connect the machine and blade, and another sensor mounts on to the blade itself. These sensors detect the position of the machine in real time. Previously this was done with two sensors, but more sensors offer improved accuracy as more data is available and the machine can perform more quickly.
Flexibility
Manufacturers like Topcon are now utilising components that are used across different solutions for both dozers and excavators. This means that there is now the flexibility to use your solution, like MC-Max, across multiple machines (after a base calibration from the installation team) without needing to purchase multiple components. The excavator configuration can also be used on drills, hammers and compaction machines while the dozer system can also be used on graders. This can give you the ability to take your projects to the next level – with increased accuracy and efficiency right across the workflow.
It’s critical to ensure there is support and training from your technology provider when taking on new technologies as it enables upskilling, resulting in your team having greater flexibility in terms of where they can use their skills across the site.
Improved health and safety
Some automated MC solutions, like the MC-Max dozer system, are now often mastless. This means that as well as being a cleaner installation, you don’t need to worry about removing 2-2.5m masts when there are working height regulations or restrictions preventing the removal of masts.
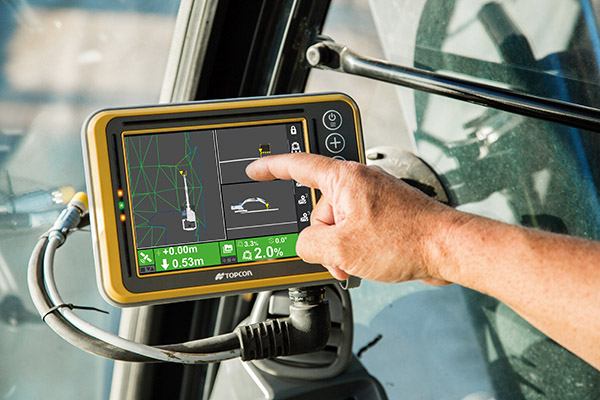
These can cause problems when they are an obstruction to specific structures that the operator needs to drive into. The main benefit of mastless systems is that operators no longer need to climb up to remove the receivers, which can be one of the most dangerous elements.
Newer machines now come with a safety guard around the top too, so that the operator can’t fall off the back. The antennas are now mounted within the safety area and there are handles and steps to maximise safety entering the cab.
Secure your site
Security is also a huge factor – older machine control solutions did have masts and obvious antennas which posed a security risk on sites – as theft can cost project owners thousands of pounds and waste a significant amount of time while sourcing replacement equipment.
While smaller sites now usually have security, bigger road and infrastructure projects, like HS2, can’t have security along the whole stretch of the works. These newer systems are much less intrusive and it’s now difficult to detect if a machine has a GPS system without the obvious poles.
Knowing that there is reduced risk of vandalism, theft and damage as well as the significant health and safety element can be a huge benefit when making such a significant investment and can make all the difference to the success of projects, with less risk of delays through damage or injury.
What does the future of machine control look like?
Automation is just the first step for the next generation of machine control. In the future, it’s likely that the whole excavation process will become automated – increasing productivity across the entire workflow. At the moment, deciding whether to use more excavators or dozers is a human-led decision, based on factors like the length of the haul or type of material excavated.
Once construction workflows are fully automated using powerful data management software like Topcon’s MAGNET and Sitelink3D, project managers will be able to accurately assess the rate of progress and resource the operation appropriately using the reports from the machines. Fully automated workflows could be the answer to meeting the increasing pressures and targets for the construction industry.
Find out more about Topcon’s automated machine control solutions at www.topconpositioning.com
This article has been produced by Construction Management in association with Topcon.