This CPD, in partnership with Topcon Positioning GB, discusses the intricacies and challenges of asphalt paving projects, and how technical innovations are changing the sector
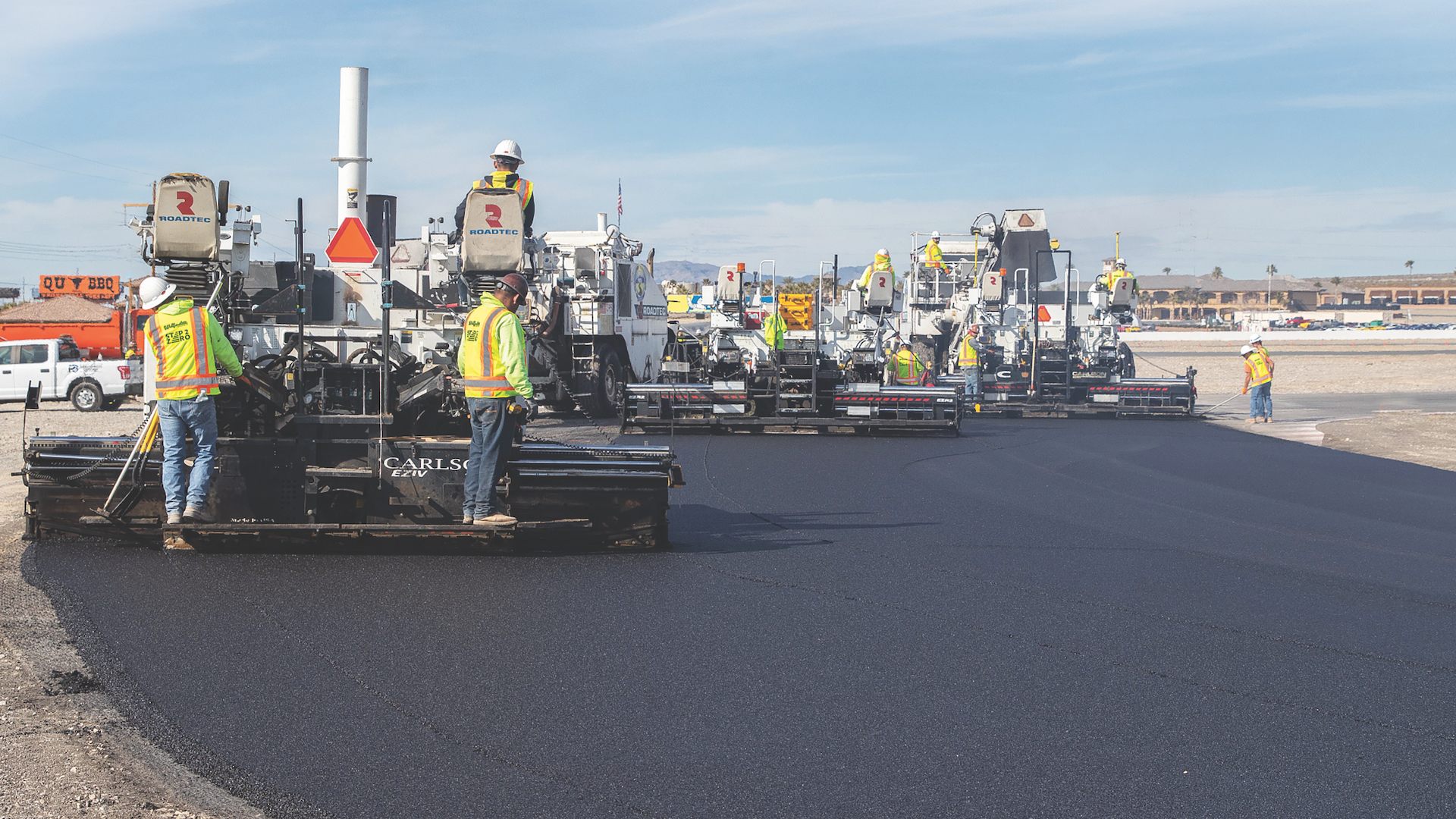
Asphalt paving projects are an essential part of road maintenance and are crucial for keeping infrastructure running smoothly.
The process involves a considerable amount of planning and designing, with issues such as environment, traffic, terrain properties, utility works, nearby residents and maintenance costs all important considerations for new road projects.
For ongoing maintenance projects, conditions of the existing roads must also be assessed, as there can be huge repercussions if the work is inaccurate – including starting the entirety of the work over again which can double a project’s costs.
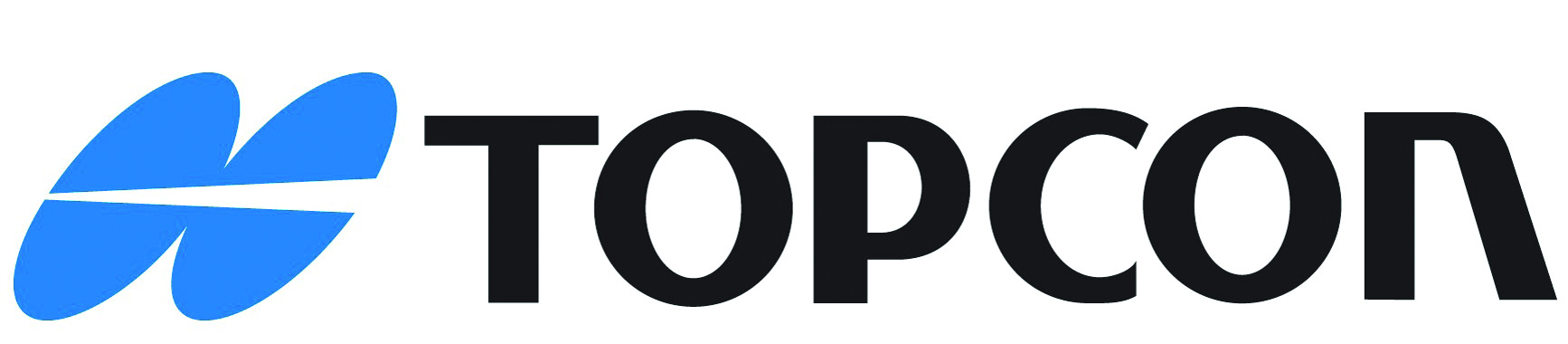
Once the initial planning and design work has taken place, excavation machinery and tracked dozers are used to move and mount a variety of materials across the entire project to give it its shape. Once completed, the area must be graded to ensure a level base.
As an industry that remains traditional in its methods, this involves a combination of manual labour and machinery, such as a paver, which is crucial in the road-building process since it not only lays the asphalt but also the large stonework foundation. This is then compacted to allow the laying of the hot asphalt sub-base, base, binder and finally the surface course layer that is driven on.
Next, the asphalt is tipped into the paver ready for the hot paving process to begin. Traditionally, to do this, an operator drives the paving machine while two screed operators follow at the back of the machine on either side, dipping a metal rod into the asphalt and checking the depth against a ruler to ensure that the correct thickness is being laid while adjusting the levels of asphalt accordingly if it is incorrect.
A further two labourers are usually also on site, to banksman the wagons to and away from the paver, and to dig out the asphalt that has been laid on top of the plates covering manholes once the paver has passed over these, as they need to be exposed.
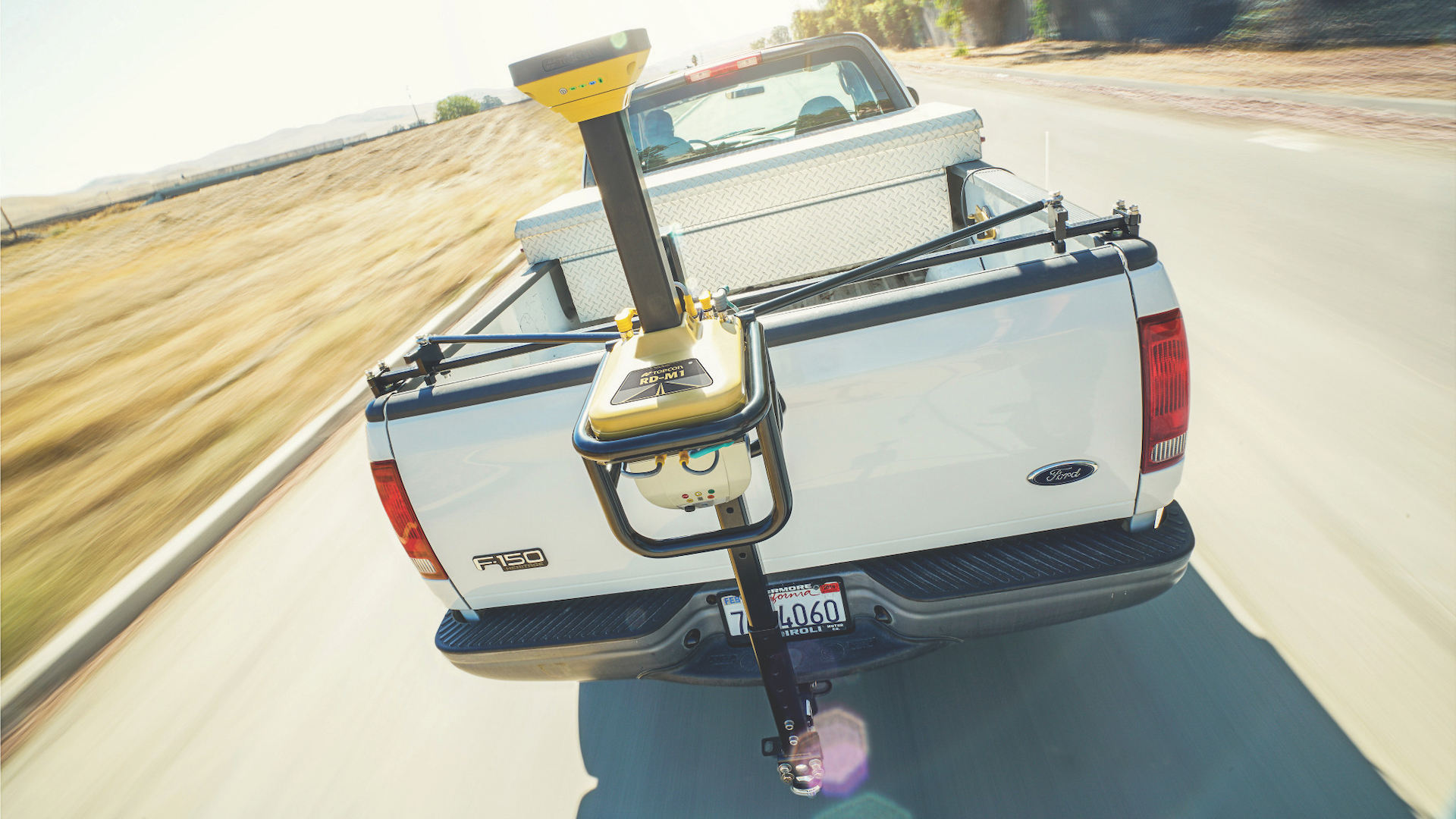
Challenges when paving
The paving process is not without its challenges. The hot mix asphalt, which is usually a bitumen compound, not only needs to be laid at the correct height – it also to be the correct mixture of compounds.
In addition, since the material needs to be the right temperature, it also needs to arrive on time, since delays can cause the material to cool in transit. If it is too cold, the bitumen is not as malleable as it should be and starts to go hard – meaning it does not bond correctly when laid.
This is called thermal segregation and can result in water entering inside the road surface, freezing and then cracking to create potholes, which then worsen when cars drive over them. To avoid this, the paving material must be laid at the correct temperature as well as the correct level.
Compacting the asphalt on the road once the material has been laid is also an important part of the process, as the material also needs to be rolled at the correct temperature. To guarantee the right temperature, compaction systems feature an in-built temperature sensor. However, if the paver ahead is paving too fast, by the time the roller with the compaction system catches up to the material, it is unable to bond together correctly.
That said, if the material is rolled at too hot a temperature, this also negatively impacts compaction as the stones in the material get pushed below the surface, resulting in less texture and skid resistance. It is critical that the rolling temperature is correct, and that the paver and roller are working collaboratively to avoid future road failure.
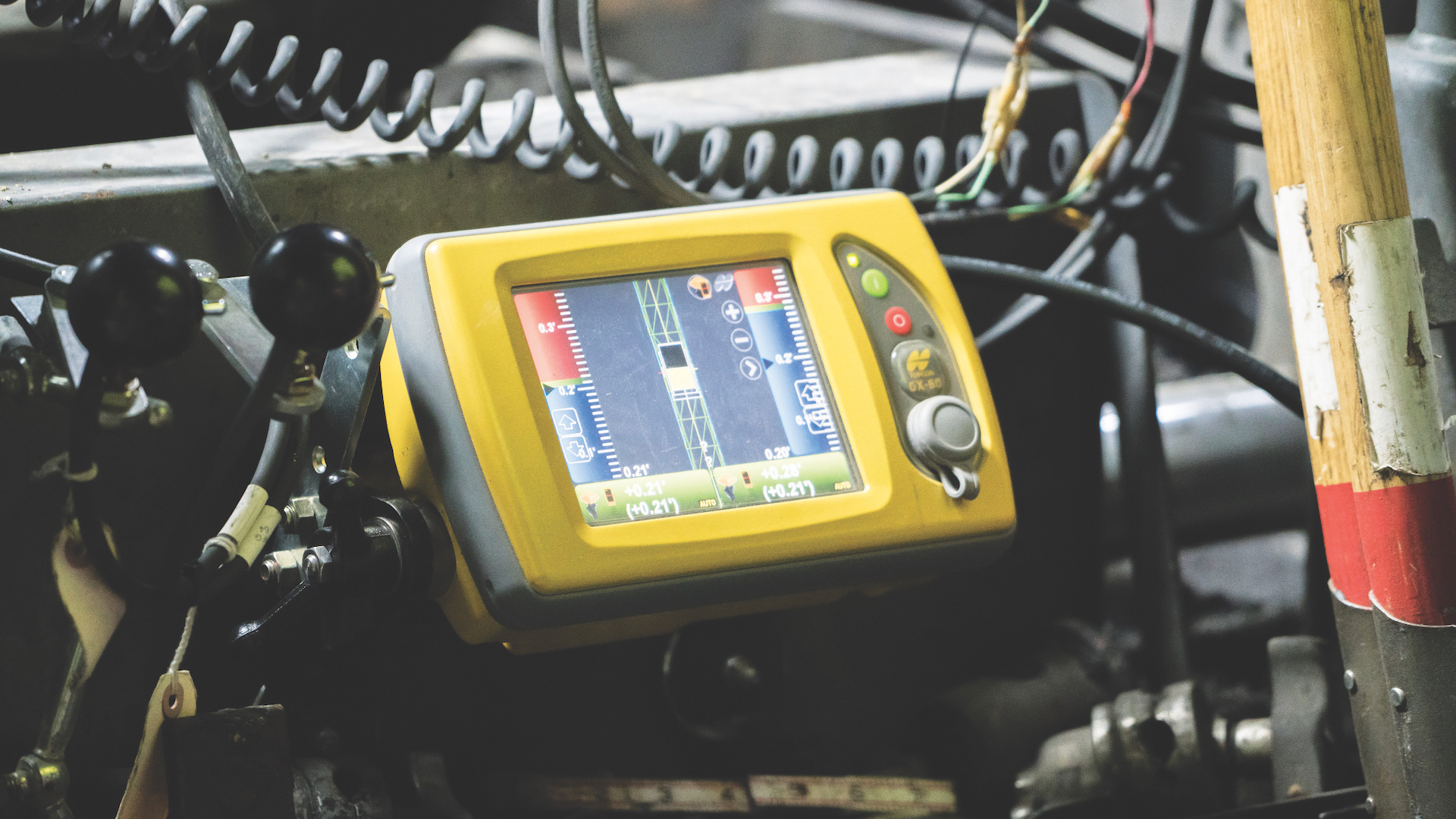
Testing the accuracy of paving
After the paving has been laid, tests must be carried out to check the accuracy of the project. The rolling straightedge test, for example, which consists of a straightedge of a fixed distance mounted on multiple wheels with a censor at the centre, is used to measure deflections in the road.
Prior to the paving being laid, accuracy requirements will be set out – usually specifying that over a 3m length, inaccuracies can be no more than 6mm. If the paving contains a depression or peak in the material that has been laid, the rolling straightedge test equipment will notify the operator.
Errors picked up by the rolling straightedge test can be one of the largest causes of paving job failures and need to be corrected so that drivers do not feel a bump in the road on their journeys.
To try to eliminate the risk of these bumps, paver operators can use 2D paving systems like Topcon’s P-32. Providing precise slope and elevation information to the screw man through a high-contract control box, Topcon’s P-32 paving system ensures operators have all the information necessary to guarantee accurate slope and material thickness.
Benefits of innovations in paving
The paving industry remains traditional in its methods and increasing the adoption of innovations on site remains a challenge. However, when embraced, technology can provide operators and contractors with long-term reassurance of their works’ precision and can offer protection if roads get damaged in the future.
This is because, when roads break down, if operators have the paving and rolling data from their machines to confirm their project accuracy, they can prove that they are not liable for any failings of the road in the future and avoid paying any penalties or completing any rework.
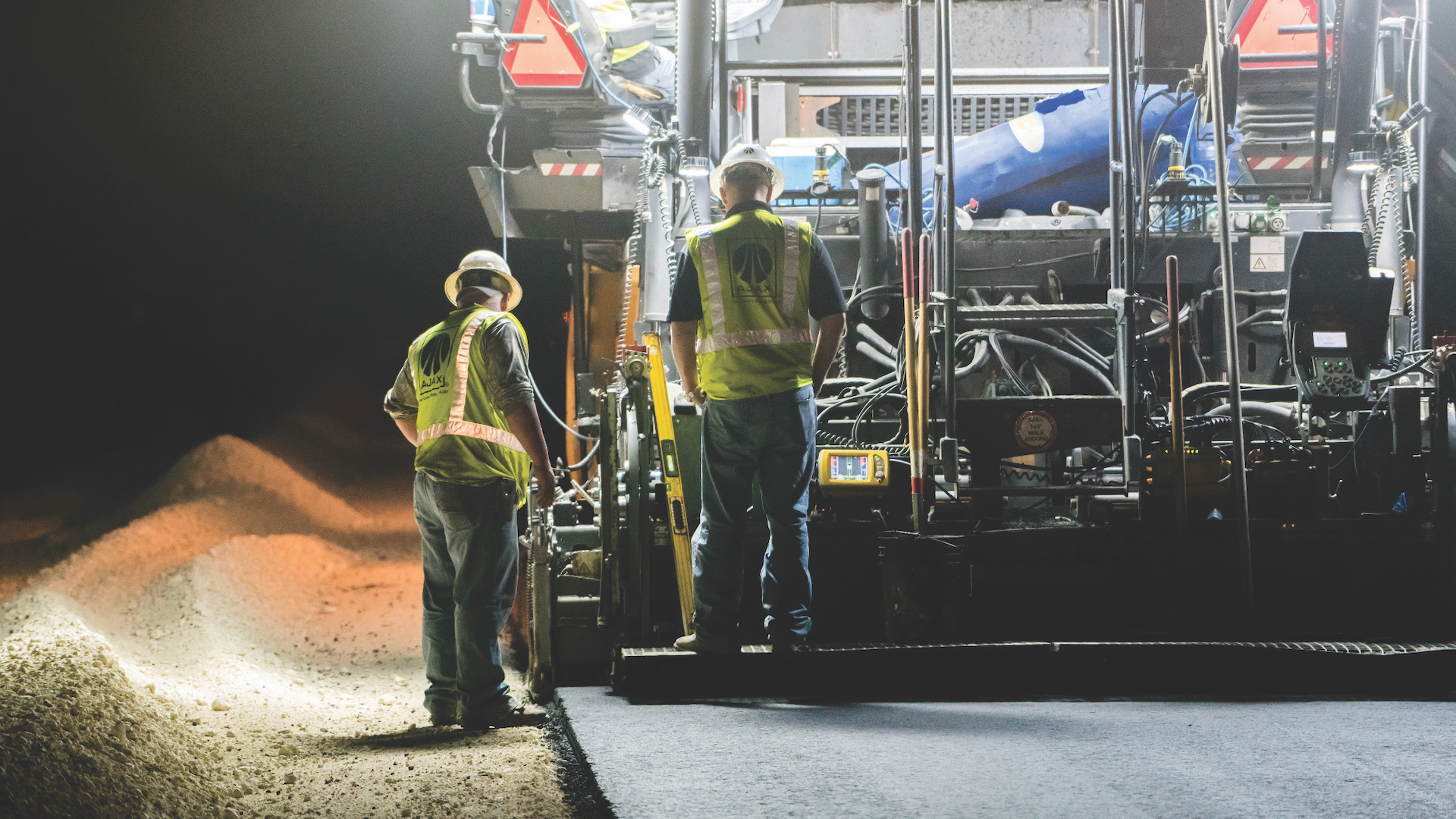
The future of paving
The future of paving lies in the adoption of technology. By recognising the benefits of innovation, there is now a huge opportunity for the industry to transform paving workflows and increase project productivity and accuracy by investing the latest road resurfacing solutions.
One such solution that is helping to maximise productivity and increase accuracy on paving projects is Topcon’s SmoothRide technology, which saves time and lowers project costs.
Beginning with the design stage of the process, the solution uses an RD-M1 scanner, which is placed on a vehicle and driven across the existing surface at around 55mph, to collect data on the millions of points on the surface and provide a complete and accurate scan of the area.
Next, using Topcon’s MAGNET Office computer software, operators can find the imperfections in the data collected by the scan – such as the depressions in the road where trucks sit, and use this information to design the changes that need to be made. These can vary from different cambers, slopes and angles to identifying where water runs off a surface. Once these changes have been identified, they can be input directly into the planer – which can then mill out and plane to the exact level and time needed.
Without this technology, the entire surface would be planed and basic equipment, like a trundle wheel, would be used to take measurements, before the different levels required for the road are sprayed onto the surface to notify the paver.
Not only is this time-consuming, it is also less accurate and efficient, as the operator doing the paving would have to keep adjusting the levels for the different material heights.
Materials can also compact differently, potentially causing issues as there are different levels of material being laid. With SmoothRide, however, the planer changes all of the levels itself using data – automatically adjusting to different heights so that the pavers can simply lay one set amount of material across the entire width and distance without needing to do any measurements.
As well as saving time, this ensures operators know how much material is needed for a project in advance, reducing waste and costs, and minimising the likelihood of rework.
For projects like airport runways or motorways, where time is tight and resurfacing needs to be done as quickly as possible, investing in SmoothRide can also have significant financial benefits, since the paving can be carried out at driving speed – eliminating the need for costly road closures.
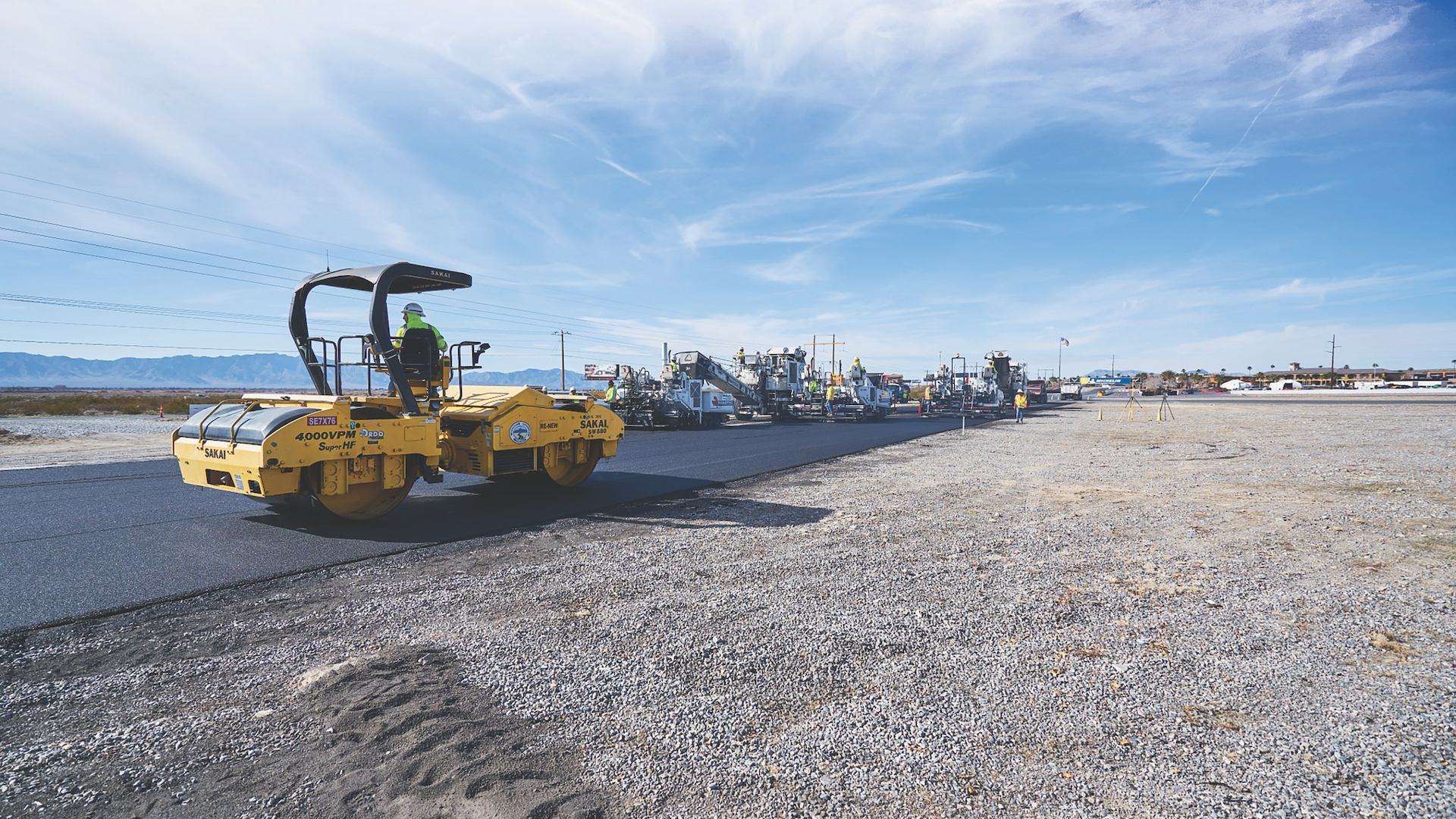
Embracing technology
Technology has the ability to revolutionise paving and significantly increase productivity and accuracy on projects. However, the challenge for the industry is convincing operators and contractors to embrace this onsite innovation.
When younger generations work on projects, there is a slight shift in favour of uptake of the latest innovations. Yet, still there are some operators reluctant to embrace even the easiest-to-use solutions, like SmoothRide, that could transform their efficiency for the better – reducing costs, saving time and providing reassurance against any potential future problems.
It will be down to leading manufacturers in the industry to highlight the benefits that new technology can bring to paving, to encourage operators and contractors to embrace innovation.
This article has been created by Construction Manager in partnership with TopCon.