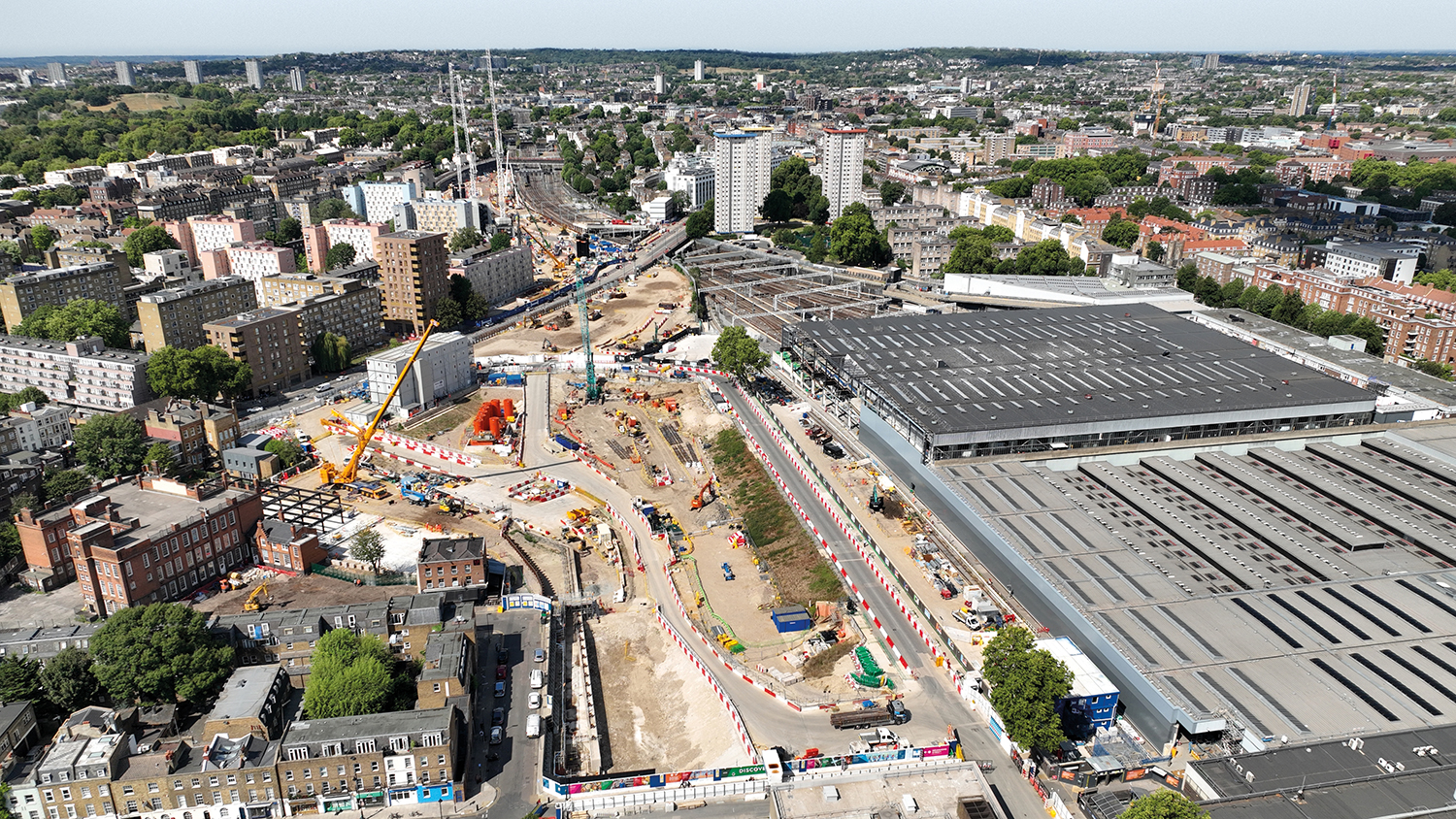
This CPD explores how the combination of advanced gas combustion technology, solar power and battery energy storage helped HS2 reduce emissions by 95%.
Diesel generators are a significant contributor to air pollution from construction sites. The National Atmospheric Emissions Inventory (NAEI) highlights the construction industry as being a key source of air pollutants across the UK, with exhaust emissions from non-road mobile machinery (NRMM) diesel equipment being a significant contributor.
What you will learn about in this CPD
- The impact of diesel generators on air quality
- What low-emissions alternatives are available
- Future developments
And a 2020 study by Imperial College London – as yet unpublished – found that generators were the highest source of oxides of nitrogen (NOx) emissions from non-road mobile machinery (NRMM) on HS2’s phase one early works programme.
According to the London Atmospheric Emissions Inventory (LAEI) 2019, construction was responsible for 4% of NOx, 30% of PM10 (particulate matter with particle sizes lower than 10 micrometres) and 8% of PM2.5 emissions within London.
The fine particulate matter in diesel engine exhaust is classed as being carcinogenic to humans and in 2004 the World Health Organisation (WHO) advised that there is no evidence of a safe level of PM exposure. Imperial College London estimated that in 2019 toxic air contributed to the premature deaths of 4,000 Londoners.
A development programme, funded by Innovate UK under the government’s Clean Air Programme, set out to create the Clean Air Gas Engine (CAGE) as a direct alternative to diesel generators for construction. The aim was to significantly reduce emissions of the pollutants outlined above together with carbon emissions.
OakTec Power, which develops fuel efficiency and emissions reduction technology, joined forces with generator manufacturer Sutton Power Engineering and site welfare specialist Advanté to develop a low-emission, off-grid, electricity generator which is built into a welfare cabin. Powered by solar panels, with backup from the bio-liquid petroleum gas (bioLPG) generator, the site cabin solution is aimed at construction contractors.
Costain Skanska JV (CSJV) trialled the new technology at its HS2 Enabling Works site in Euston. Onsite testing by Imperial College London quantified the emission-saving potential of this solution in comparison to conventional diesel alternatives. The results were impressive, delivering up to a 95% reduction in emissions.
Clean Air Gas Engine technology
Large-scale industrial gas engines with low emissions already exist. However, the engines used on site for generators, pumps and other machines are relatively small and clean gas engines of that size are not currently available.
To plug that gap, the CAGE development programme focused on engines between 2kW and 60kW, taking various pieces of technology developed for other applications and putting them together so they could be applied to commercially available engines. The rationale behind this approach was that it would be too costly to develop brand new engines and would take too long – when the technology is needed now.
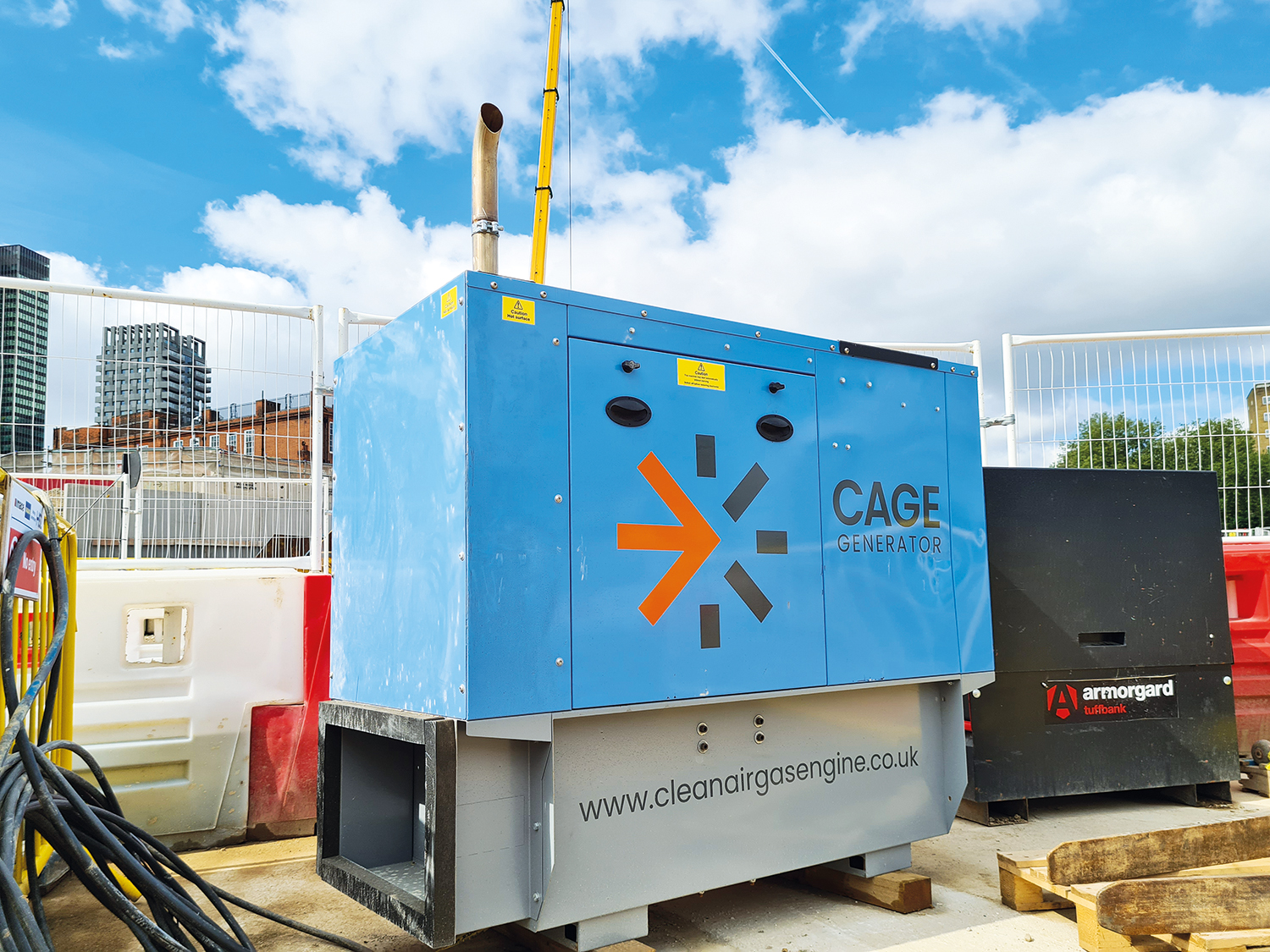
The CAGE concept takes advanced digital control combustion strategies for gas fuels and applies them to simple industrial engines. The objective is to run a precise combustion regime using lean air-fuel ratios, which leads to NOx emissions being very low. The precise control of load demand, fuelling and ignition together with a fast response to external conditions allows the combustion to be held in a narrow band of air-fuel ratio over the full operating cycle of the engine.
This combustion strategy eliminates carbon monoxide (CO) emissions and significantly reduces NOx at source while keeping hydrocarbons and particulates to a minimum. Hence, a basic low-cost industrial engine can be transformed into a highly sophisticated and precisely controlled gas engine with digital control of fuelling, ignition and load, and intelligent response to ambient conditions.
The bioLPG engine was integrated into Advanté’s patented telemetry-controlled solar battery hybrid power system to create off-grid site welfare units built for the project. The site cabins optimise the use of renewable energy while minimising engine operation hours and, through use of battery power storage, allow the engine to only operate at its cleanest and most efficient.
The hybrid solar and bioLPG system reduces engine use from 24/7 for a conventional diesel system to between one and three hours per day, the highest use being in midwinter. The engine only engages when the battery state of charge is low.
BioLPG, sometimes called biopropane, is created from a range of biological feedstocks including cooking fat, animal fat, vegetable oil and food waste. It has the same chemical composition as LPG but a carbon footprint up to 90% lower.
Results from the trial
Trials of the engine integrated into the Advanté welfare unit began on CSJV’s HS2 site at Euston in November 2020 and ran for 12 months. The onsite welfare unit consisted of an office area, canteen, charging and drying room and toilets and was extensively used by the site teams throughout the trial.
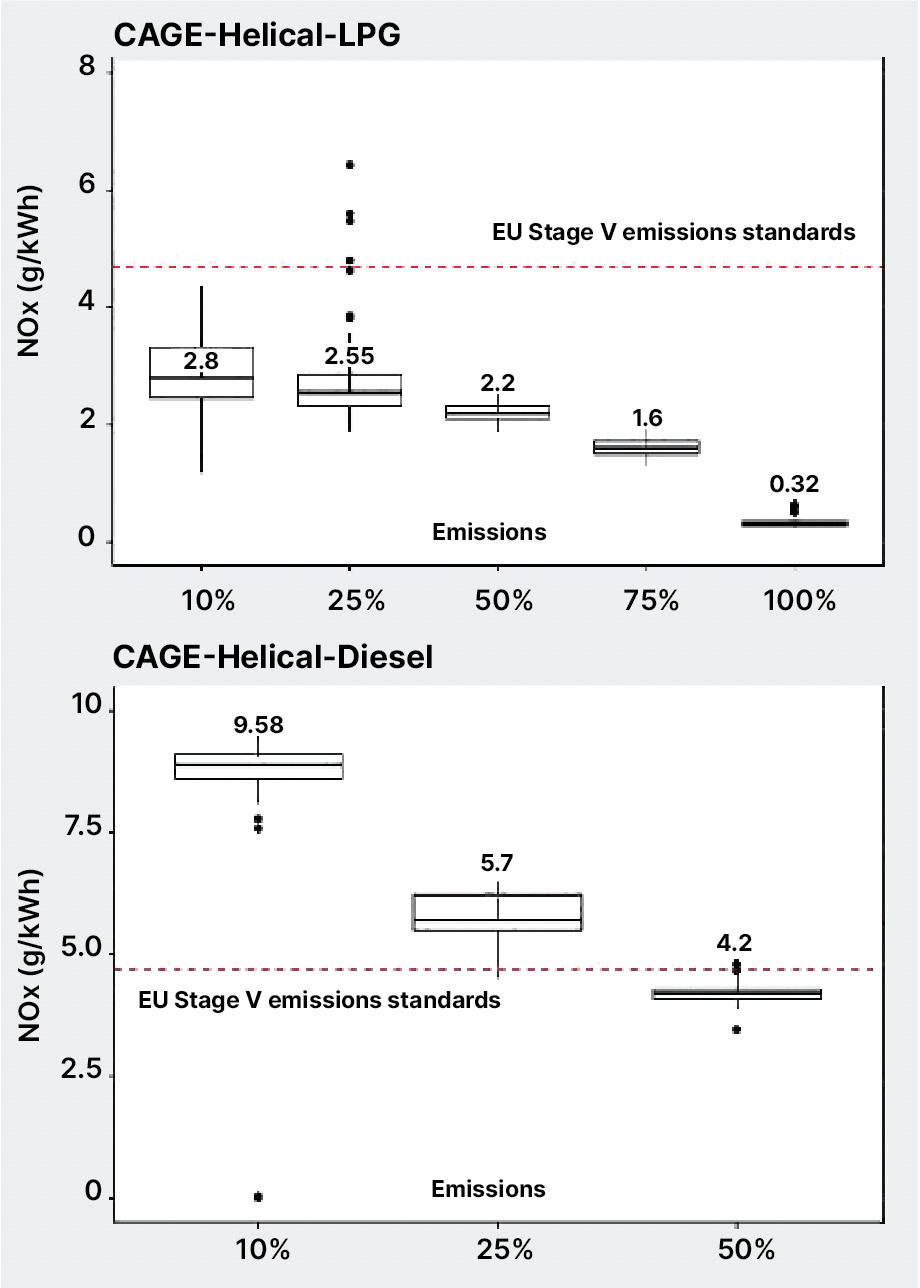
The welfare cabin operates silently on stored energy and uses Advanté’s EcoLogic curfew technology to limit noise during unwanted hours to further reduce negative environmental impacts for operatives on site and people living in surrounding local communities. The trial delivered a total power consumption of 359kWh over the period, with 74kWh or 21% of the power consumption coming from the CAGE and the remaining 79% coming from solar energy.
Load profiles and gas usage on the trial were remotely monitored. Emissions were measured on site by Imperial College London and in the laboratory at the Helical Technology research facility, so that emission savings compared to a diesel-powered generator could be calculated.
The CAGE trialled on HS2 emitted 20% of the emissions allowed by the EU Emission Stage V standards without requiring costly after-exhaust treatment systems to be fitted. Stage V is the current, and most stringent, emission standard set by the EU, which has been ramping up emission standards for engines over the past two decades through a series of directives.
For the Stage V emissions test, an aggregate of the components of CO, hydrocarbons (HC) and oxides of nitrogen (NOx) are taken from the exhaust emissions during a regulated engine test cycle. The CAGE was tested on this cycle and benchmarked against a directly comparable liquid-fuelled engine that meets the 2020 Stage V standard. Tailpipe sum total emissions reductions of CAGE vs the Stage V engine were as follows: CO 99.5%, HC 86%, NOx 20%.
The results demonstrated that the CAGE was below the EU emission Stage V standards – 4.7g/kWh for NOx and HC (indicated on the graphs above by the dotted red line). The diesel engine was above the same emission standards for
the first two load points.
When the CAGE was integrated into the solar hybrid system with automatic stop-start, there was an overall emission reduction, including CO2 of up to 95% compared to a conventional diesel engine running in the same application.
Future developments
In addition to reducing harmful emissions, including carbon, this combination of solar energy and bioLPG allows the generator to run continuously with no downtime needed for refuelling. It is also currently cost-competitive with red diesel, according to OakTec.
The trial was the first of a series of gas engine innovations and emission reduction technologies which OakTec is developing for the construction sector. The next step was a higher output multi-cylinder engine, a development of the latest three-cylinder Jaguar Land Rover automotive unit tested in a 27kW generator at Euston in 2022. Rather than diesel, it uses directly injected bioLPG and automotive standard after-treatment.
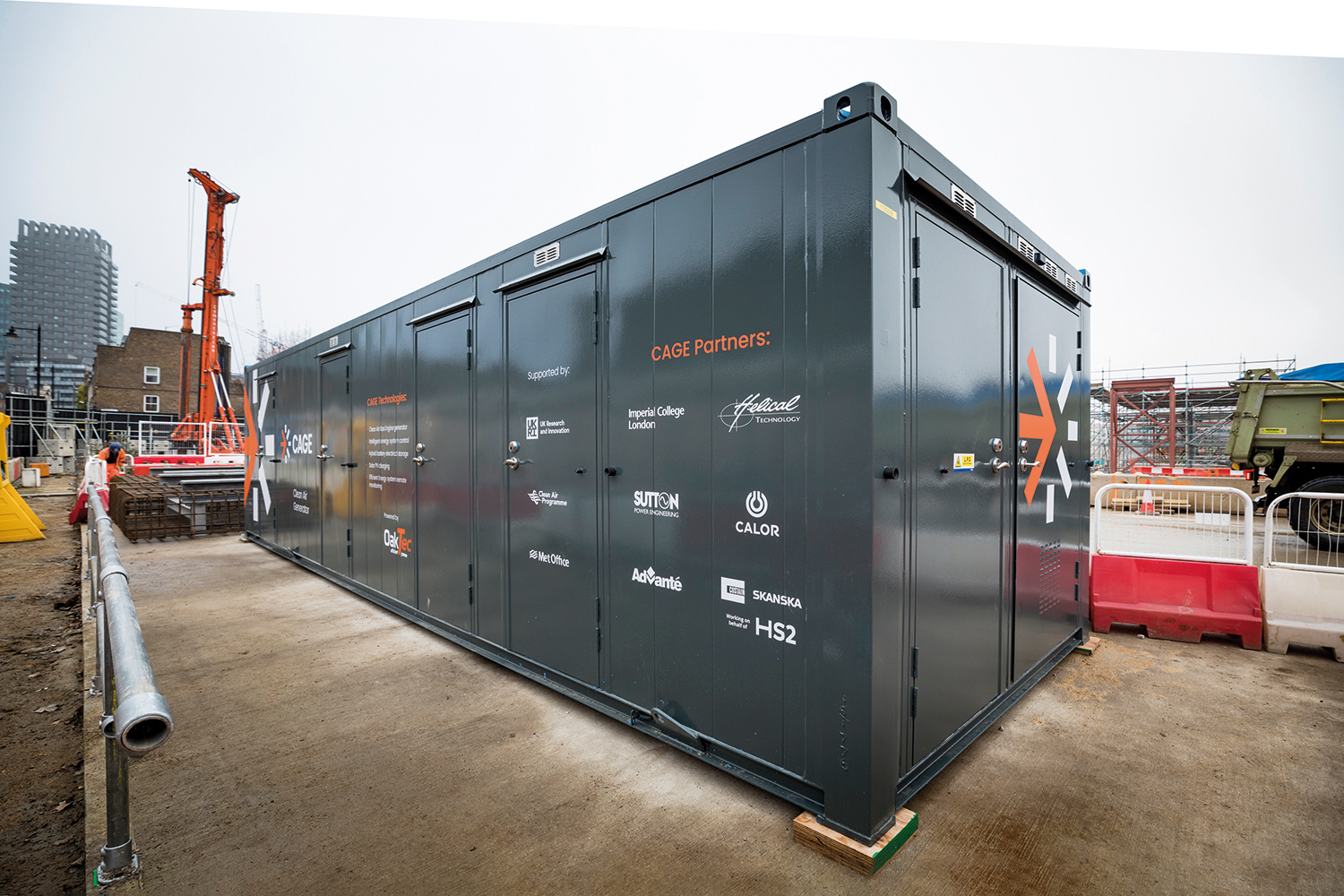
A new OakTec company, CAGE Technologies, was formed to commercialise outputs from the CAGE project and those of parallel biogas and hydrogen-related development programmes. The project also saw the establishment of a dedicated laboratory to enable certification of industrial engines, the first of its kind in the UK. This is based within the Helical Technology research facility.
CAGE technologies could have widespread applications and can be used in many applications currently served by diesel and petrol engines within construction and other sectors. Building power systems using CAGE CHP (heat recovery) is another major opportunity for the technology.
OakTec is now working with hydrogen engine prototypes to develop a complete net zero
solution that would work in applications such as welfare units.
The authors of the original paper are: Andrea Davidson, air quality manager, HS2 (Jacobs Engineering); Neil Wait, head of environmental sciences, HS2; Daniel Marsh, programme manager, Centre for Low Emission Construction, Imperial College London; Carl Desouza, PhD research assistant, Centre for Low Emission Construction, Imperial College London; Paul Andrews, founder and CEO, OakTec; and Stan Chapman, research and development director, Advanté.