With accidents and fatalities on the rise, Brenig Moore provides a reminder of how construction should be managing workplace hazards.
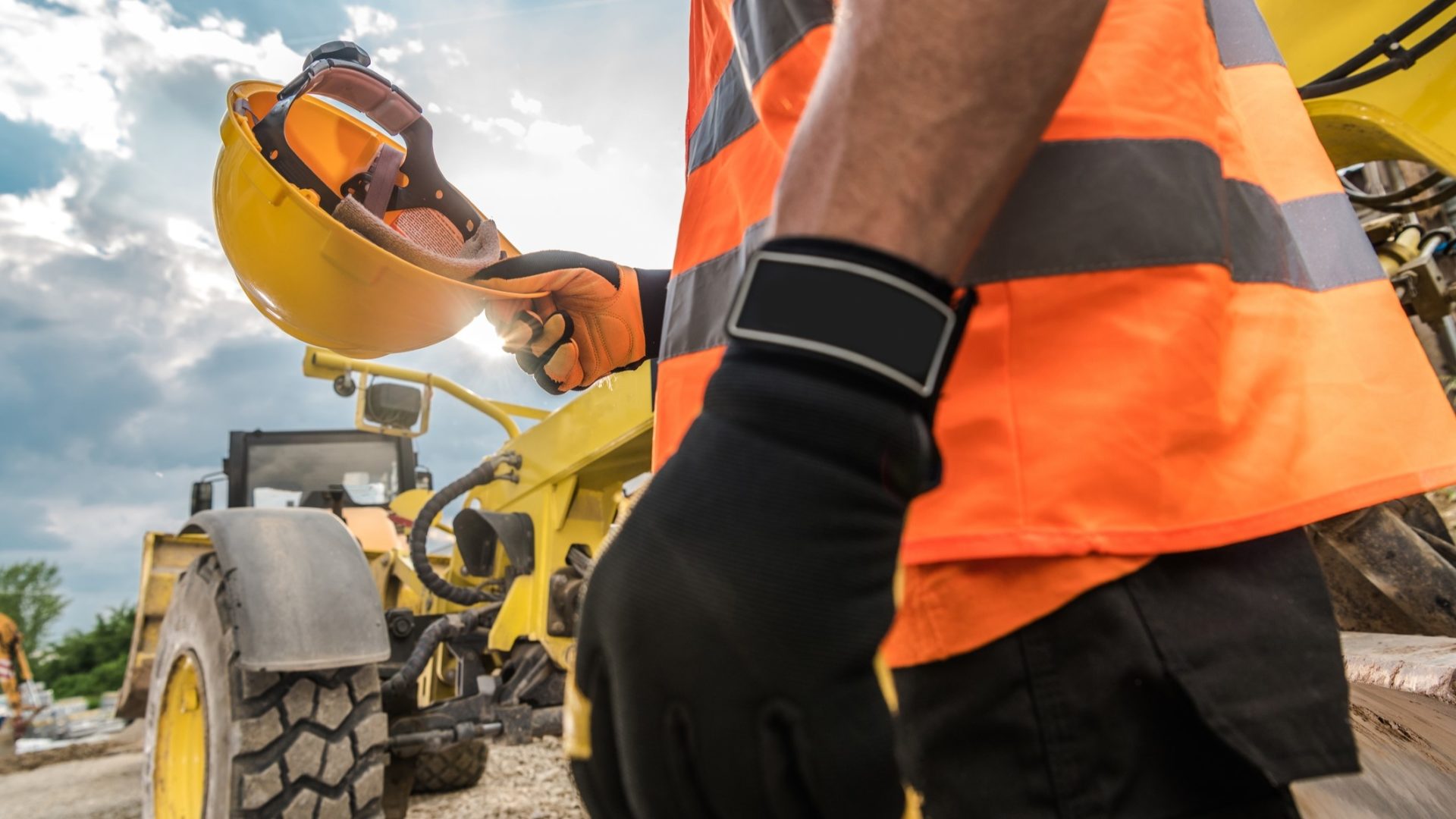
The latest Health & Safety Executive figures for construction show there were 45 fatal injuries and 53,000 non-fatal injuries during 2022/23.
That means the industry killed 16 more people than in the previous year – a worrying rise. The figures indicate that construction needs to pay closer attention to workplace hazards and how they are managed.
What are hazard controls?
Hazard controls cover any measures that protect construction workers or members of the public. These should be a given on any construction site, but sometimes they are missing. Some of the most common hazard controls include:
- Engineering controls. Physical controls to protect workers, for example guardrails to prevent falls, machine guards, noise protection for loud machinery.
- Personal protective equipment (PPE). The last line of defence for workers: hard hats, gloves, safety glasses, high vis vests, safety footwear, hearing protection or harnesses. Everyone on site should know how to use them correctly.
- Fall protection systems. Falls from height are the most common cause of fatality. Safety harnesses, nets, and other precautions are essential for work at height.
- Hazardous material controls. Construction involves working with dangerous materials like cement, lead, solvents, isocyanates, and carbon monoxide. Project managers should swap out risky materials where possible, follow manufacturer and industry guidance for handling hazardous goods, and use ventilation.
- Emergency response plans. This means being ready for fires, building collapses, medical emergencies and any other eventualities. Evacuation plans, first aid stations, and emergency training are the key.
- Regular inspections and maintenance. Keep an eye on all equipment, machinery, and work areas that will be used.
- Communication and collaboration. Openly talk about safety concerns with everyone from director level to site workers. Safety committees and toolbox talks are a great forum to discuss and find solutions as a collective.
- Administrative controls. Policies, procedures, safety reports and work practices keep risks in check – as long as they are kept up to date.
Safety reports for construction sites
Construction projects also need a ‘playbook’ for maximum safety and that’s the safety report. It keeps all the project workforce in the loop about potential risks. Safety reports should include:
- Basic details. Name of the project, when it is taking place, which companies are involved and who the key points of contact are, and what the project goal is.
- Hazard analysis. Break down the risk, include photos if needed, and present the information in a user-friendly way.
- Digital reports. Safety reports should include real-time data and be compatible across platforms, so they are easily accessible for all workers.
Hazard controls and safety reports are important proactive ways to manage active risks on construction sites. It is better to take the initiative and identify a hazard and take the necessary action rather than have it found during an inspection, audit or – worse – an accident. This all takes time – but think of it as an investment in the safety of everyone on site.
Brenig Moore is technical director of health and safety training provider Astutis, which delivers courses through CIOB Academy.
UK legislation and regulations that cover workplace hazards
- Health and Safety at Work etc Act 1974
- Management of Health and Safety at Work Regulations 1999
- Workplace (Health, Safety and Welfare) Regulations 1992
- The Health and Safety (Display Screen Equipment) Regulations 1992
- The Manual Handling Operations Regulations 1992 amended 2002
- The Regulatory Reform (Fire Safety) Order 2005
- RIDDOR (Reporting of Injuries, Diseases and Dangerous Occurrences Regulations 1995)
- The Personal Protective Equipment at Work Regulations 1992
- COSHH (Control of Substances Hazardous to Health) 2002
- The Provision and Use of Work Equipment Regulations 1998 (PUWER)
Comments
Comments are closed.
Fall protection systems. The hierarchy of risk control would require you to consider fall PREVENTION first, before fall protection since some of the controls listed can lead to other hazards, eg. safety harnesses and suspension trauma.