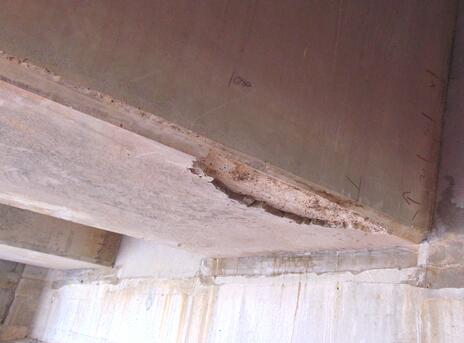
Safety experts have raised concerns about poor manufacturing processes and inadequacies in the product certification of precast bridge beams.
Collaborative Reporting for Safer Structures UK (CROSS-UK), a platform that allows construction professionals to share information confidentially about structural safety risks, said it was concerned these issues were becoming “an increasing problem in the industry”.
The warning came after an experienced bridge engineer reported concerns over the quality of precast prestressed bridge U-beams installed on a recent project.
Their quality was so poor that they needed to be replaced.
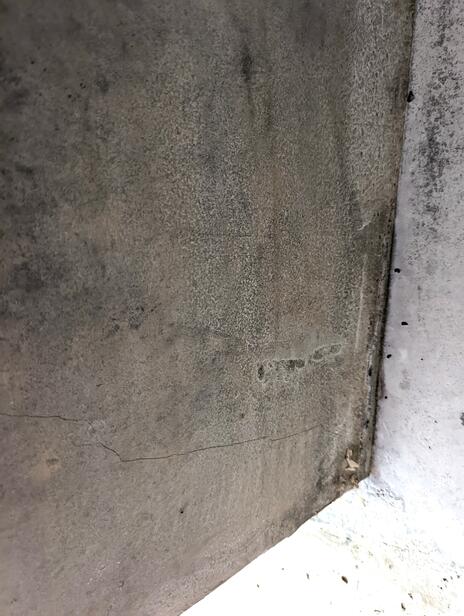
The beams showed many visible defects consistent with poor quality control and workmanship in the mixing, placing and compaction of the concrete.
The reporter saw evidence of delamination and debonding of the concrete at a cold joint and proof of inadequate bond between the pours.
They also noted significant areas of honeycombing to the beams, to the extent that one beam leaked when the U-section was full of water.
Given the extent of visible defects observed and the apparent poor quality control, the reporter was concerned about defects that could not be observed.
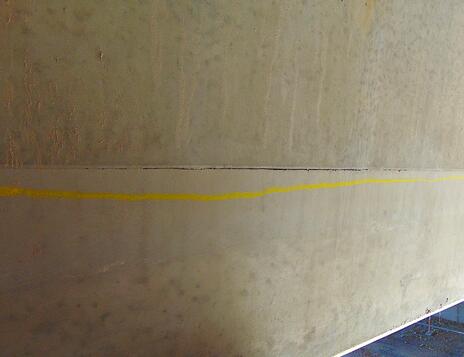
Product certification
The engineer also highlighted inadequacies in the product certification process (specifically and generally).
The reporter confirmed that the beams had all relevant certification, including being UKCA/CE marked to EN 15050:2007 (+A1:2012) Precast concrete products – Bridge elements, which is a designated standard in the UK.
CROSS-UK pointed out that UKCA/CE marking simply confirms the declared performance and not the general quality of a product.
However, part of the process (according to the standard) includes a visual inspection which should have flagged some of the defects before the beams left the factory.
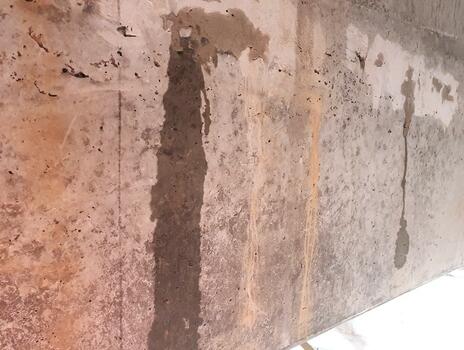
‘Cultural shift’ needed
CROSS-UK expert panel members said they were aware of similar issues on high-profile projects where precast concrete quality is poor and has led to the rejection of units.
Examples of the 14 faults mentioned by the panel include casting concrete prior to approving drawings, misaligned formwork, excessive blowholes and areas of poor compaction, debris in the base of pours, and omission of chamfers and fillets.
The expert panel said the issues described in the report put into question whether clients and designers can rely on self-certified quality assurance (QA) and quality control (QC) systems and called for a “cultural shift”.
“QA and QC can descend into pedantry, but at their heart is a system that seeks to ensure that these events do not occur,” the panel said.
“Clients do not fully appreciate the value of independent inspection; issues need to be identified and resolved in the factory before they become costly and expensive problems during installation or whilst in use.
“If a product is specified to a particular quality, that is for a reason. If it is asserted that it has been manufactured to that quality, it should be verified. Independent checking provides that reassurance.”