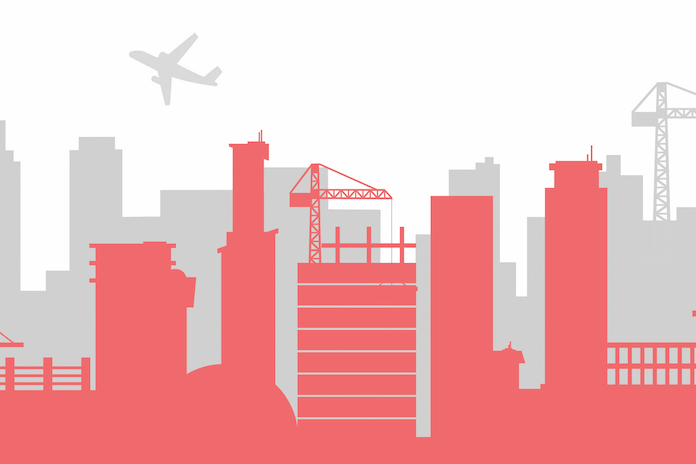
Image: Dreamstime
A study into common project failings finds the same issues cropping up time and again. Dan Keeling and Dr Diyana Abd Razak explain
Dame Judith Hackitt’s Independent Review of Building Regulations and Fire Safety in 2018 identified quality issues in construction which many feel should have been resolved long ago.
Over the years, many improvement initiatives have been recommended, but the focus on final product and ensuring the customer gets what it specified have not been adequately addressed.
Taking the airport sector alone, Heathrow Terminal 5 had a disrupted opening, costing British Airways £23m in the first five days, Charles de Gaulle airport had a roof collapse, while Brandenburg Airport finally opened in October last year – 10 years late – after being plagued by construction problems.
The Chartered Quality Institute (CQI), with University College London (UCL), has investigated how successfully projects delivered what was required from a client’s viewpoint on completion, and the financial cost of poor quality.
Five projects were studied in detail using interviews with clients, contractors, quality teams, plus operations and maintenance staff.
The results do not make pretty reading. A £150m car park project suffered from poor drainage design and installation, with rectification and lack of availability costing £15m. A water treatment plant failed to function as promised, resulting in a quality cost of half the contract value. And a £50m airport runway resurfacing led to issues with design, construction and maintenance, which cost over £4m to put right.
These problems are sometimes reflected in safety incidents which then get significant attention. However, the root cause – quality – tends to be overlooked.
There are number of endemic issues the study identified.
Procurement strategies, frameworks and contractual arrangements set by clients lead to a fragmented construction industry. There is a ‘blindness’ among the senior leadership teams of both clients and contractors about the operational impacts of not focusing on quality. And architects and designers feel no ‘pain’ from quality issues, either on site or during operations – when they are usually far removed from the project.
What can be done to address this persistent poor quality? The performance of the project and its delivery strategy should not be based only on programme time, cost and quality but also the operational performance of the asset. Client, architect, designer, contractor, subcontractor should work in a single team. Because of the misalignment of their goals, the whole system becomes fragmented leading to operational failure.
Hackitt identified four key issues that underpinned the system failures in the construction industry: ignorance, where regulations and guidance are misunderstood or misinterpreted; indifference, where the primary motivation is to do things as quickly and cheaply as possible; ambiguity and lack of clarity about roles and responsibilities; and inadequate regulatory oversight and enforcement.
This study backs up her findings. These systemic problems occur across the building and infrastructure sectors, but they start at the top. Clients cannot pass responsibility down the supply chain and sit back expecting all to be well; they need to lead on quality.
Dan Keeling was head of quality at Crossrail and is now a senior associate with Shirley Parsons. Dr Diyana Abd Razak is a lecturer in construction management at Kingston University
Comments
Comments are closed.
One of the points missed, is procurement. This section goes to all sorts of checks before a contractor is registered on a clients Framework or appointed. However, this exercise is only on paper, the procurement people never get to see any of the contractors previous works, and they normally choose a contractor who charges more than other contractors. Why does procurement ask, demand some of the most complicated requested conditions you have ever seen and hence good contractors give up. There are many companies out there who also carry out credit, work and H&S checks why are procurement getting involved. To many cooks syndrome! Resolve the procurement issue and you may get more quality lead contractors and less contractors who are good at answering questions on paper and less competent at giving quality.