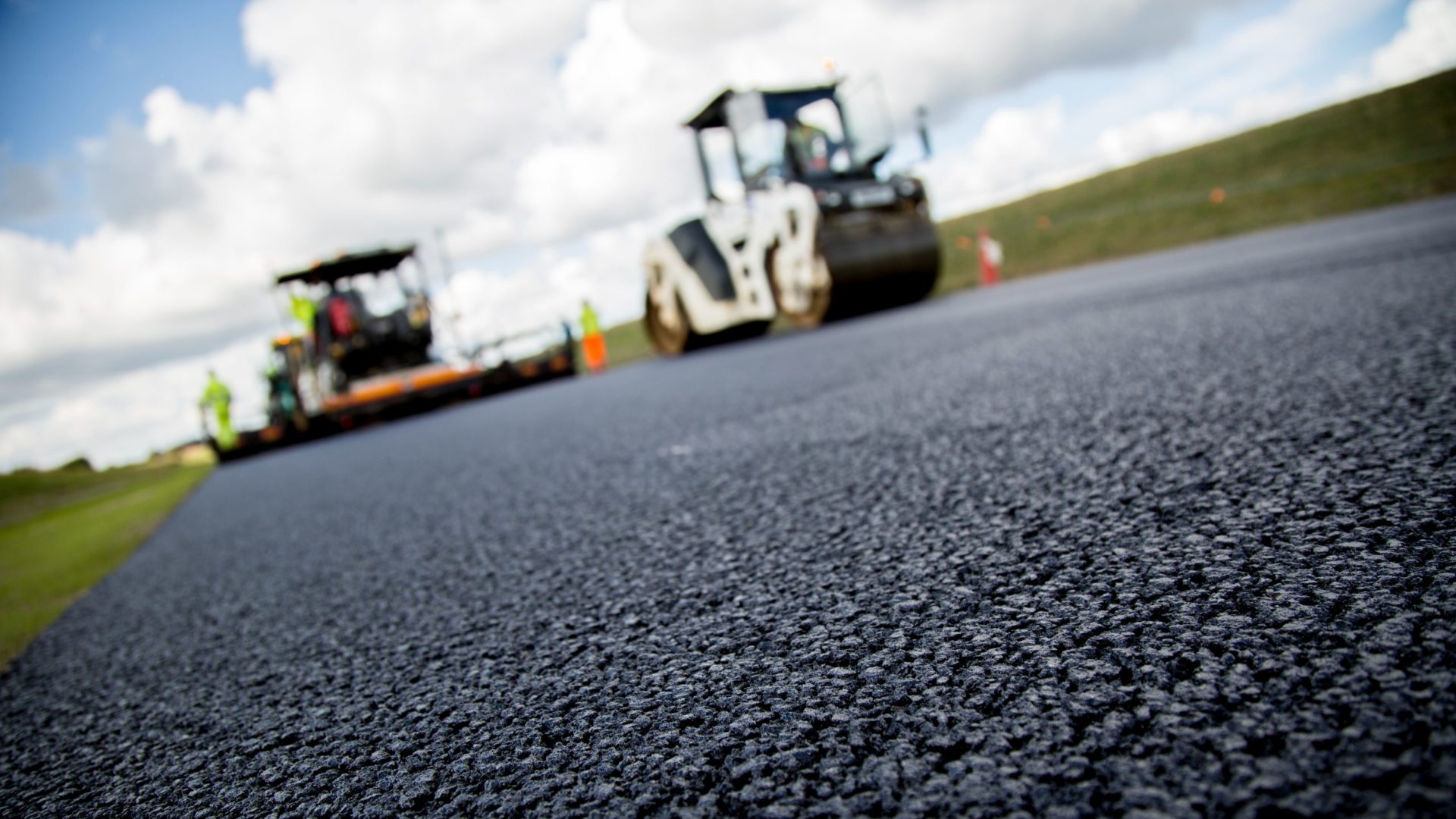
With local authorities spending millions every year in maintainig roads and filling potholes, Tarmac’s Brian Kent examines sustainable solutions that can help fixing the problem in the long-term.
The latest annual local authority road maintenance report by the Asphalt Industry Alliance estimates that the cost of repairs needed to bring roads across England and Wales up to scratch is at a record high, at £14bn.
Breaking the cycle of repeated deterioration with better-quality materials requires significant investment. But so too does a never-ending programme of running repairs.
More than 300 councils in the UK declared a climate emergency by the end of 2021 and legislative targets to reduce emissions across all sectors continue to loom.
If we also consider the volatility of energy prices worldwide, finding more sustainable methods of construction without impacting cost becomes a priority. And the construction sector should be finding ways to deliver those repairs more cost- and energy-efficiently.
Addressing the challenge
Using conventional methods of road repair across more than 200,000 miles of local roads in England and Wales (97.3% of the total road network) would do little to support the sector’s net-zero efforts.
It would do little to support whole-life performance too. A tendency to place a heavy weighting on initial cost can neglect consideration of the longer-term value of the whole-life performance of pavements.
Manufacturers and contractors are increasingly turning to innovative solutions to reduce carbon emissions and environmental impact, both in the short-term repair phase and ongoing lifecycle of the road network.
Identifying the solutions
There are many aspects to consider when building more sustainable roads, from using lower-carbon materials and reducing waste during construction, to incorporating more recycled content and specifying products that will reduce future maintenance requirements. Many of these solutions are not necessarily new.
Tarmac switched production of selected mixes to warm mix asphalt in July 2022. Warm mix asphalts are manufactured and supplied at lower temperatures than conventional hot mix asphalts. This can reduce carbon dioxide emissions and lower carbon production. Tarmac’s Ultilow warm mix saves up to 15% of CO2 compared to conventional hot mix asphalts.
This lower temperature material also enables road projects to be delivered faster than when using traditional materials. The asphalt is delivered cooler than hot mixes, taking less time to reach trafficking temperature. This means that the road can be opened to traffic up to 90 minutes earlier, reducing disruption for road users.
Recycled content
We have also been investing in ways to increase the percentage of reclaimed asphalt planings incorporated in asphalt across the Tarmac asphalt plant network. In addition, Tarmac’s Ultifoam recycled foam mix asphalt provides safe encapsulation of tar contaminated road plannings that would be excluded from hot mix asphalt recycling and otherwise be considered hazardous waste requiring costly and specialist disposal.
Tarmac incorporated recycled rubber from end-of-life car tyres to asphalt in 2019, helping to recycle some of the 40 million waste tyres generated every year in the UK. Tarmac’s rubber-modified asphalt was used to resurface the A426 in Leicestershire. It recycled rubber from approximately 3,500 tyres and saved 14 tonnes of CO2 emissions.
Single layer materials
Another way those responsible for highways maintenance can reduce the carbon footprint of carriageways is through the specification of single layer materials when work is required below surface course level. By using one single layer instead of the traditional two layers, less material is removed from the carriageway.
A whole life approach
Innovation has created a portfolio of materials specifically designed for a range of challenging applications. Correct material selection and specification acceptance is a priority as we seek to address the challenges around sustainability and investing in the future of our road network.
The industry is investing in materials and processes to enable this – now it is time for councils and contractors to embrace such innovation and see the benefits.
Brian Kent is national technical director at Tarmac