Matthias Gropp explains the role that advanced monitoring techniques, AI and IoT can play in retrofitting projects involving historic assets.
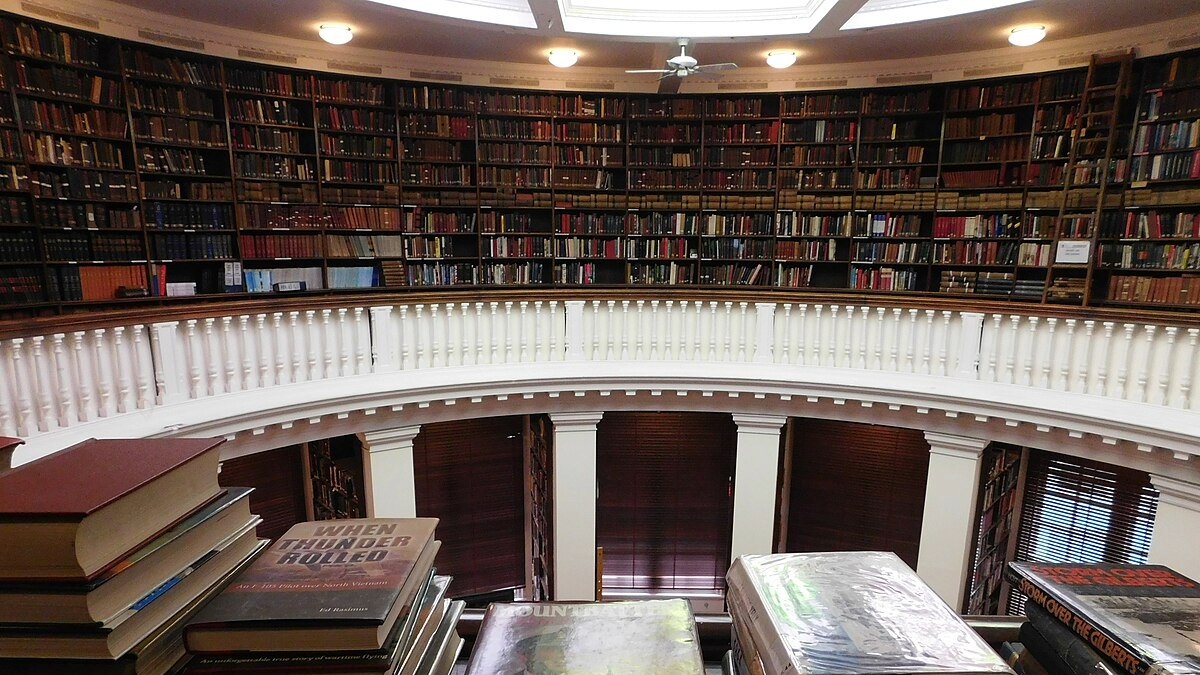
Retrofitting the UK’s existing assets is a key priority not only for sustainability and ensuring these structures adapt and change as our lives evolve, but also for the rich heritage that exists within the walls of these assets.
With over 370,000 listed buildings in England alone, preserving historic buildings is a crucial task. However, their age brings a host of challenges, from structural integrity issues to energy inefficiencies.
Listed buildings are particularly vulnerable to damage from vibration, moisture ingress, or ground settlement during nearby works or refurbishment. Consistent monitoring is therefore an essential step in their preservation and mitigates the risk of project delays and damages.
Challenges of historic building preservation
Dampness is a major concern for historic buildings, as it can lead to structural damage if left untreated. Poor drainage and overflowing gutters exacerbate this problem, potentially causing subsidence. Furthermore, draughts from old windows and doors, coupled with outdated insulation, reduce energy efficiency. The electrical systems in these buildings also often need significant upgrades to meet current safety standards.
The impacts of climate change further complicate preservation efforts. Record-breaking temperatures and increased rainfall in 2024 have placed additional stress on these structures. Temperature fluctuations cause materials to expand and contract at different rates, leading to structural weaknesses. Increased rainfall and flooding pose significant risks, with historic rainwater systems often unable to cope with the deluge, leading to water ingress and interior damage.
The role of advanced monitoring in preservation
Advanced automatic sensor monitoring solutions, such as those we deploy at Murphy Geospatial, are essential for addressing these challenges.
These systems provide real-time feedback on critical structural parameters such as concrete strain and timber moisture, ensuring safety, compliance and efficiency in both preservation and new construction projects. By integrating environmental and structural health monitoring, these solutions offer a comprehensive approach to maintaining the integrity of historic buildings.
For instance, vibration monitoring during construction activities, such as piling or demolition, ensures vibrations remain within safe limits. Remote glass vibration monitoring can discover loose window panels. This protects not only the public and neighbouring structures, but also the historic buildings themselves. Additionally, monitoring concrete temperature and strain provides vital data for engineering decisions, ensuring the longevity and safety of these assets.
Enhancing capabilities through IoT and AI
The integration of internet of things (IoT) technology and artificial intelligence (AI) is revolutionising asset management because engineers can get direct feedback on the performance of their assets.
IoT sensors stream data continuously, which AI analyses to predict potential issues and automate responses. This predictive capability supports proactive maintenance, preventing problems before they arise and reducing the need for reactive repairs.
Asset performance monitoring (APM) leverages these technologies to provide continuous oversight. APM enables the integration of diverse monitoring solutions into a custom maintenance plan, enhancing operational efficiency and asset longevity. For construction and infrastructure sectors, adopting APM can extend the lifecycle of assets, reduce maintenance costs and ensure high-performance levels.
Matthias Gropp is director of monitoring at Murphy Geospatial.
Case Study: RUSI, 61 Whitehall, London
A prime example of advanced monitoring in action is our work on the Royal United Services Institute (RUSI) building at 61 Whitehall, London.
During this Grade II*-listed building’s extensive refurbishment, Murphy Geospatial was tasked with providing environmental monitoring solutions throughout site demolition, excavation and construction.
Murphy Geospatial installed a vibration monitoring network at strategic locations to monitor the vibration and acceleration of the party walls adjacent to the Welsh Office and Banqueting House. This was crucial to ensure compliance with British Standards. The monitoring setup involved highly precise three-axis vibration sensors that reported measurements through a cellular network to a central database daily.
The project involved staged installation of the monitoring equipment, with baseline monitoring conducted for six weeks before the main contract works. The final outputs included peak particle velocity, vibration dose value and acceleration, with synchronised waveform recording on all active channels.
The meticulous monitoring ensured that all construction activities were within safe vibration limits, protecting the structural integrity of the historic building.