The Digital Construction Awards attracted more than 140 entries, 62 of which have been shortlisted. Here we detail the shortlist for the Contractor of the Year category.

This category, sponsored by Procore, recognises the contractor – main contractor or specialist – that has demonstrated excellence and transformed their business through the adoption of digital methodologies and technologies.
Six entries made the shortlist this year: Kier, Graham, Mott McDonald Bentley, Taylor Woodrow, Browne Construction and PCE.
Digital by default | Kier
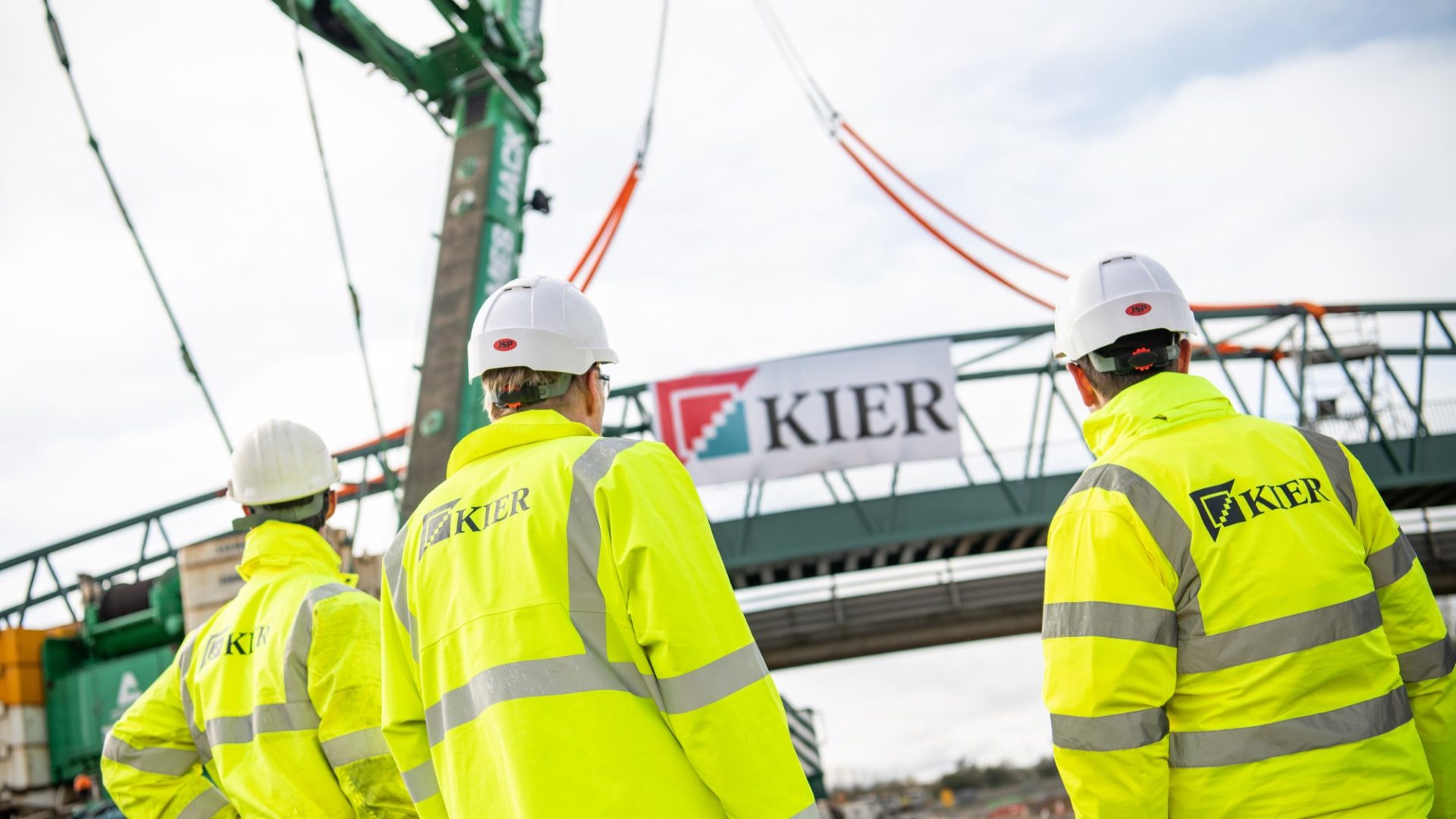
Kier’s ‘Digital by Default’ strategy has promoted a digital-first culture and behaviours across one of the UK’s biggest construction groups, leading to rewards in terms of skills, project delivery, safety, sustainability and business growth.
The strategy highlights the need to innovate and identify new technology to bring into the business, with an in-house solutions and technology onboarding process to support implementation. This includes a three-phase approach where Kier firstly establishes a genuine business driver, assesses the market for suitable solutions and then identifies the most suitable tool. The group conducted a “bring out your dead software review” that helped with rationalisation and resulted in a £800,000 reduction in software costs.
Among the new software introduced, Kier has used its quality management tool Procore to integrate photographic evidence from HoloBuilder with quality and safety activities, providing streamlined and instant access to information. The contractor adopted Asite as its principle CDE solution which allowed it to develop an information management solution which delivers statutory and legislative compliance in line with ISO 19650.
Kier has vast MMC experience and to ensure a platform for growth, it established an online library of repeatable components, pre-loaded with key object data including embodied carbon, cost, and specification. This supports its kSchool design platform and it has extended this methodology into the custodial and defence sectors.
The contractor has also used digital technology to improve the safety on its sites, using drones to monitor and improve behaviour, while reducing the need for manual labour in hazardous surveying conditions and minimising rework and waste.
Browne-Digital | Browne
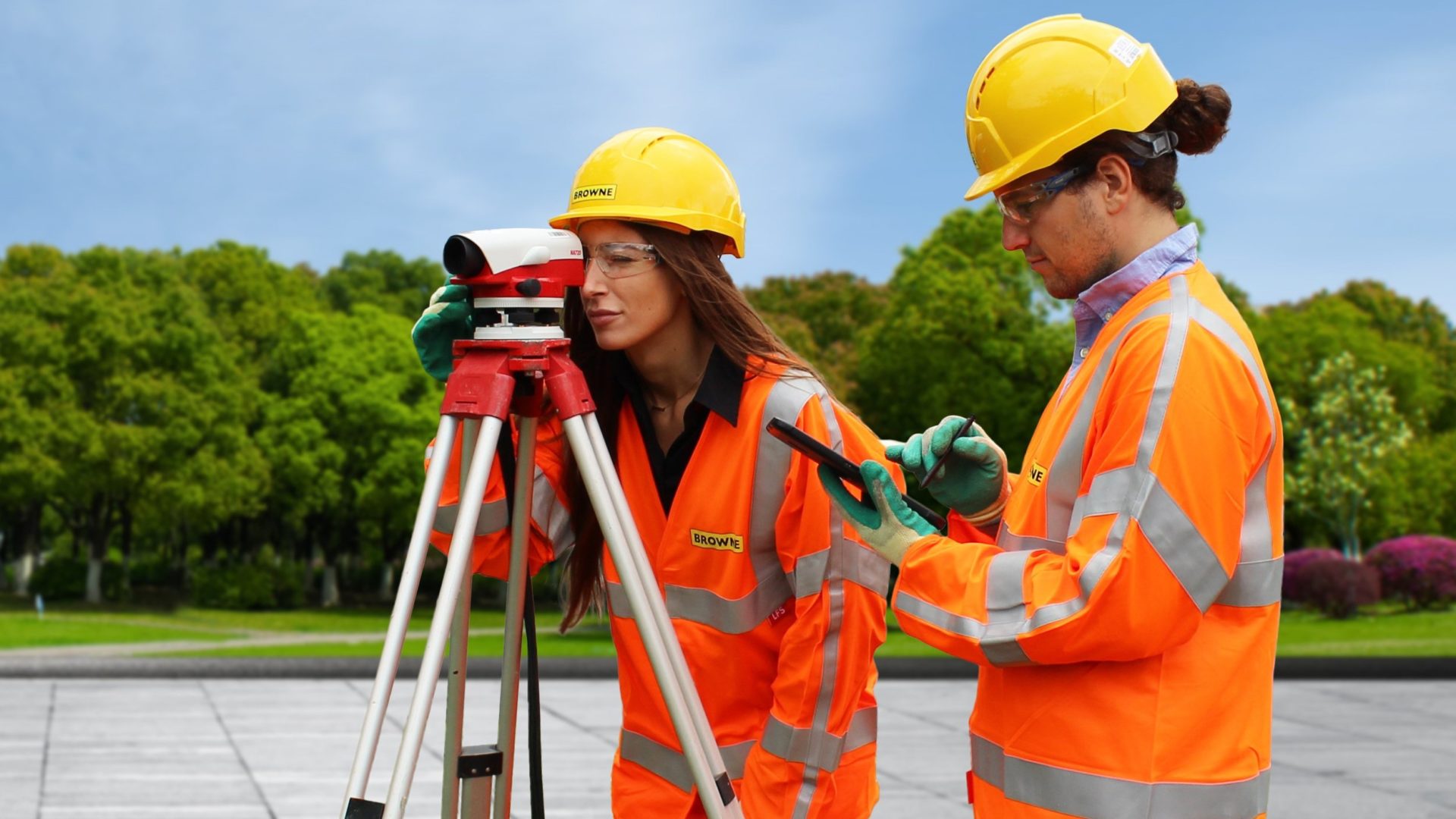
Browne is a specialist water contractor with an annual turnover of £95m. Last year, it implemented Browne-Digital, with the aim of integrating digitally enabled work practices throughout the organisation.
A challenge for the contractor was that it often served as a conduit for data exchanged between numerous project stakeholders, which historically meant the potential for human errors to be introduced. Browne’s solution was to use Microsoft Azure data warehouse to act as a hub for clients’ and suppliers’ systems, while maintaining seamless data connectivity and a clean data environment.
The ‘lowest common denominator’ approach of the Microsoft platform significantly improved Browne’s client adoption, reduced licensing complexity, and improved collaboration throughout the supply chain. It also allowed Browne to harness the work done by its ‘citizen developers’, who the company develops with online training and AI tools such as ChatGPT.
Tools that Browne has successfully introduced include Sentinel, a digital permit risk management system, which helps address the underground safety risks faced by operatives in the utilities sector. Sentinel uses information from Browne’s data warehouse plus survey data, utility drawings and photographs to produce significant measurable benefits, including a 80% decrease in traceable service damages.
Sentinel is used in conjunction with SiteEye, which is used by operatives to capture handover documents. Upwards of 100,000 photo records have been recorded in the system. For Browne’s mains replacement programmes, SiteEye has reduced the average lag between construction finishing and handover to less than one month, compared to lags of over a year in previous regulatory cycles.
Site Centric & Graham asset intelligence digital transformation programmes | Graham
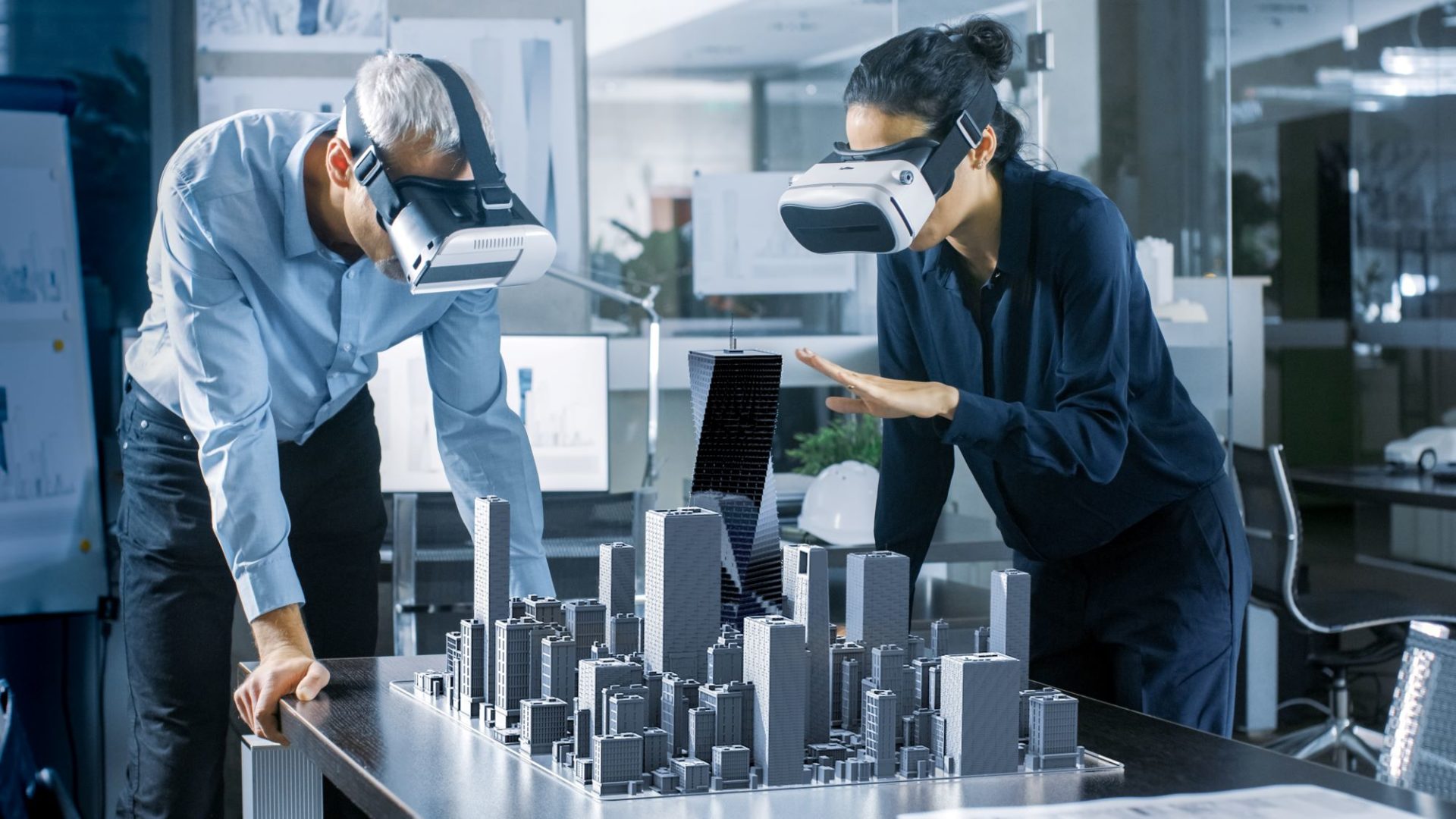
Graham decided to re-evaluate its digital strategy during 2022 and made a conscious decision to put its site teams at the centre of its thinking. The result was the introduction of its Site Centric Initiative and the Graham Asset Intelligence System.
The new strategy was prompted by a desire to remain agile and innovative in its use of data analytics and on-site digital solutions, while meeting the growing digital requirements of its clients, such as the golden thread, in a more sophisticated way.
SiteCentric aims to improve collaboration, engagement and connectivity for its site workforce. One of its initiatives is a progress tracking solution allowing visualisation of projects including their live status. This means programmed activity can be viewed close to real-time (within 1.5 hours of completion of the activity), compared to a traditional eight-to-10-hour delay in reporting.
Site Centric also included the implementation of H&S Cora – a bespoke health and safety solution that allows real-time logging of observations, accidents, disciplinaries and root cause analyses reporting.
Graham has engaged and upskilled over 500 people through Site Centric, while increasing collaboration, improving site connectivity 40%, and delivering measurable and repeatable efficiency gains scaled across operations, including reducing site data processing time from hours to minutes.
Graham’s Asset Intelligence System is a cradle-to-grave solution covering the full asset lifecycle, overhauling traditional processes for managing reactive repairs and planned preventive maintenance. It adheres to ISO 19650 and golden thread principles and is fully auditable and transparent, allowing all asset information to be visible to clients.
Graham now has the capability to offer full integration with its clients’ CAFM systems. Dashboard reporting enables visibility of large and complex client estates, acting as a window into critical data.
In the last year, Graham has processed over 200,000 requests using the system, through a direct interface with its clients’ asset records, allowing the contractor to mobilise an instant response. Benefits include a 400% reduction in time spent on planned preventative maintenance. Future developments could include the development of artificial intelligence asset models to predict the likelihood of asset failure.
Mott MacDonald Bentley
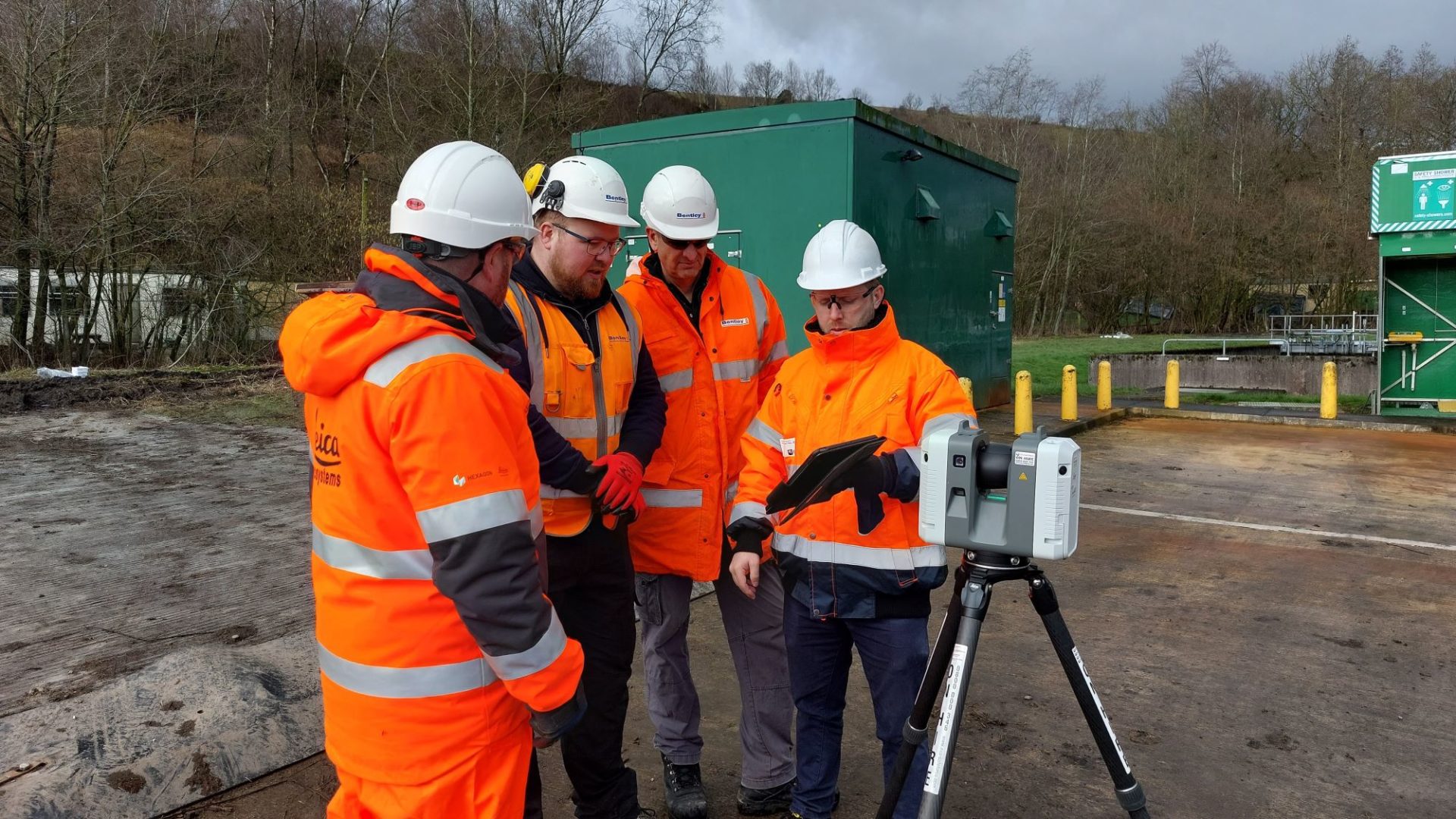
Specialist water contractor Mott MacDonald Bentley (MMB) works on projects ranging from £100,000 to £50m, and central to business strategy is its new Digital Delivery Plan.
This has involved rolling out a range of new tools to help project delivery, while encouraging suppliers to work within its CDE and providing an ISO 19650 education programme.
Using Autodesk BIM360 as its CDE, MMB gives site teams access to graphical data models prior to construction, to comment on buildability and safety issues. Any changes are made before work starts on site.
MMB teams set out directly from model data using Leica iCON CC80 handsets paired with TS16 robotic total stations. The contractor liked iCON’s ability to cloud connect to the CDE and its display of .IFC models. Since adoption of the Leica technology and digital workflows, MMB has achieved a 100% ‘right first time’ success rate in setting out, while the CDE has led to an 80% reduction in time taken to approve and issue construction information.
MMB also uses drones, terrestrial laser scanners and simultaneous localisation and mapping handheld laser scanners to collate data for definition, temporary works, and as-built survey data. The contractor has employed AR to visualise assets that are to be built, using Unity’s Visual platform due to its ability to work on our phones and tablets.
As its highest costs are during the construction phase of projects, MMB employs Synchro 4D for a digital rehearsal. On the contractor’s Ufton Nervet wastewater project in Berkshire, this rehearsal allowed a re-sequence of the works, removing 10 weeks from the programme.
PCE
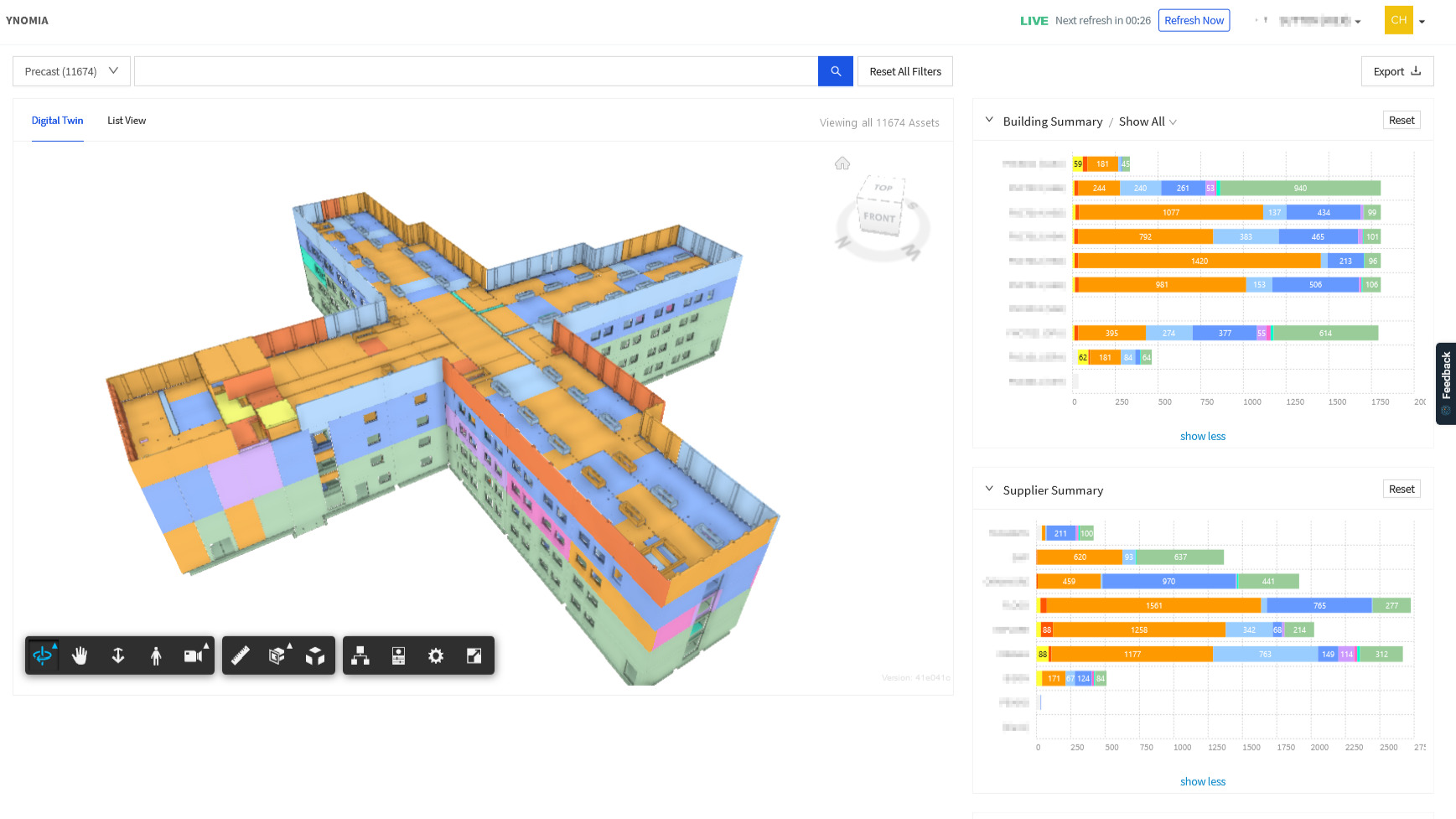
PCE is an innovative design and build contractor, specialising in the superstructure and façade, using design for manufacture and assembly (DfMA) based on a hybrid ‘kit of parts’ approach. Digital tech is key to its HybriDfMA strategy.
The contractor wanted to introduce a tracking system to provide real-time visibility on the status of projects, from design through to construction, and track potentially hundreds of components across its supply chain factories and construction sites.
After a lengthy search, it brought in Ynomia, a company that has reimagined tracking through Bluetooth and 3D digital twins. Ynomia has introduced a web platform with real-time access to crucial project information – which it takes from PCE’s Revit model – and a 3D digital twin for visualising project progress, through colour-coded statuses.
Ynomia also brought in a mobile app for rapid data collection, Bluetooth tracking tags for automated data collection and access, and Bluetooth gateways for real-time tracking of deliveries. QR codes on the Bluetooth tags can be scanned to view a component’s history or input data, minimising the risk of human error.
With Ynomia’s tracking system in place, PCE now has a digital twin that visualises its entire design, manufacturing and assembly process in real time. The contractor’s previous method of tracking the arrival and installation of components took in excess of five minutes per delivery. The new process takes just seconds, and with up to 40 loads arriving on PCE sites each day, this is a considerable productivity saving.
Let’s get digital | Taylor Woodrow
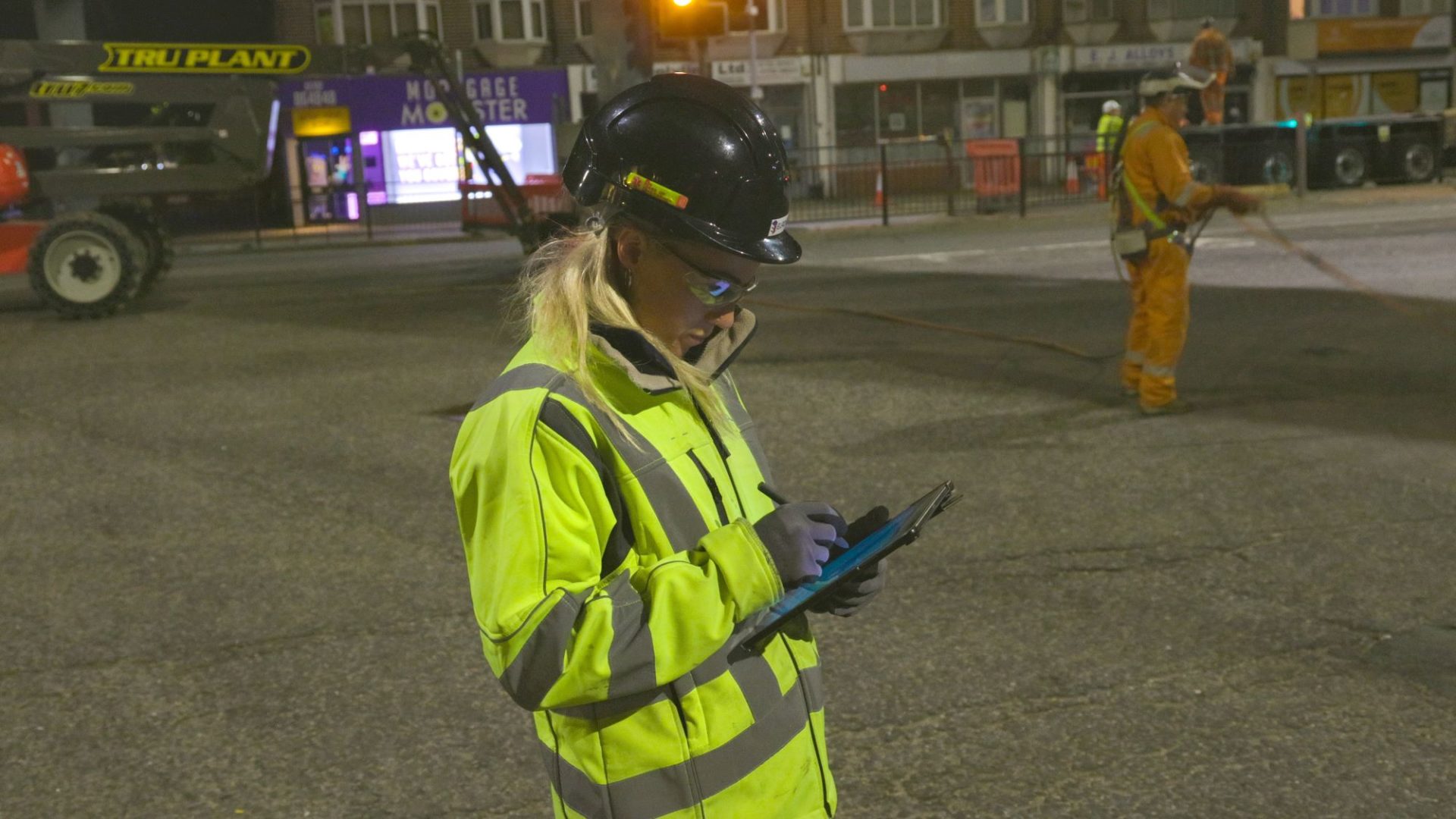
Taylor Woodrow’s digital transformation strategy, ‘Let’s Get Digital’, is already providing benefits for the infrastructure contractor, following a two-year introduction phase.
The company knew that UK government and statutory clients were pushing for the adoption of the ISO 19650 information management standard, but also felt that new digital ways of working would improve efficiency, cut silo tendencies, and harmonise IT systems across its projects.
The overarching target of ‘Let’s Get Digital’ was to instigate a digital procedural mindset throughout core business procedures in compliance with ISO 19650. Other features of the strategy include a new digital protocol for contracts with clients and supply chain, a new suite of digital procedures for the management and governance of CDEs, and a new system to define LOIN (level of information need) for every design stage.
Resources are organised through a new workforce management system platform, which automatically tracks the location of Taylor Woodrow employees. This has saved at least four hours per month in administration time giving a cost saving of £2,400 pounds per project per year.
Reporting across all disciplines, including commercial and productivity, now uses the Azure stack and Power platform. This is reducing time spent on report production by 24 hours per month compared to previous spreadsheet-based processes, plus eight hours for data capture per site. This has meant a saving of £134,000 pounds across 32 projects.
Taylor Woodrow has also introduced a digitised quality assurance process which provides a transparent, auditable, searchable system, which it estimates has provided reporting efficiencies totalling 2,200 hours.
Celebrate with the best
The winners of the Digital Construction Project of the Year category, alongside the victors of the other 11 categories, will be revealed at the awards dinner on 4 July at the Brewery in London.
You can join them by booking your places at the awards. There is an early bird discount for those who book tables before 5pm on 19 May.
The Digital Construction Awards celebrate best practice and reward innovation in the application of BIM and digital technology in the built environment sector.
The awards are run by Digital Construction Week, the Chartered Institute of Building, and Construction Management and BIMplus.
Awards sponsors include the Association for Project Safety, BIMcollab, Bluebeam, Everwarm, Graitec, nima, Procore, Revizto and Sir Robert McAlpine.