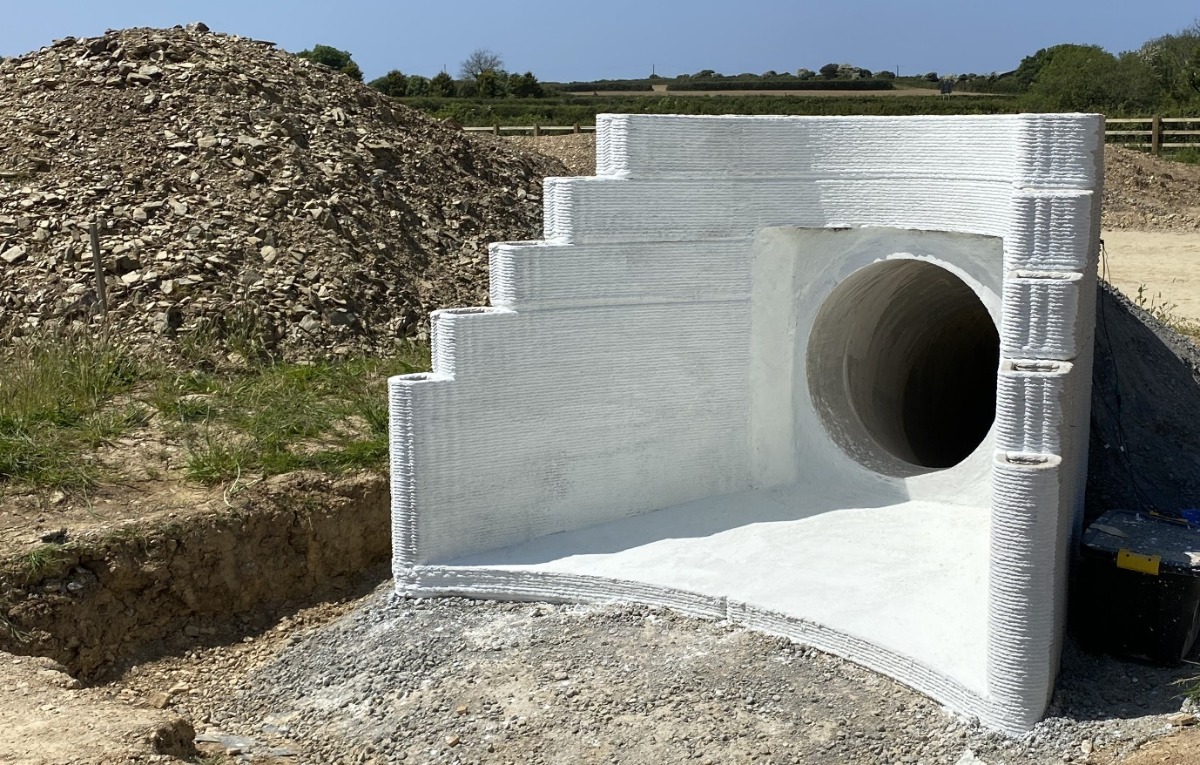
The first-ever 3D-printed concrete headwall is being tested as part of the construction process of National Highways’ A30 Chiverton to Carland Cross upgrade in Cornwall.
Headwall structures are traditionally made from precast concrete, using extensive steel reinforcement, and limited in their shape. However, the 3D-printed curved headwall requires no steelwork. Costain installed it last month as a trial on one of the project’s under-road wildlife crossings.
Once complete, the scheme will provide 33 multi-species crossings along the length of the new 8.7-mile dual carriageway.
The project is part of the Digital Roads of the Future Partnership, a collaboration led by Costain with partner company Versarien, the University of Cambridge and National Highways. It’s the first trial of its kind for the agency.
The 2.3t headwall is constructed using an alkali-activated cementitious material and a 3D printer.
The first trial headwall was printed at Versarien’s Gloucestershire operations centre in December. During the printing process, Cambridge University researchers embedded a number of sensors into the structure to provide temperature and movement data.
Gathering real-world data
A headwall was chosen for the trial because of the ease of access for installation and monitoring.
With the headwall in place on site, without affecting the operational highway, PhD students and post-doctoral researchers from Cambridge University will gather real-world data.
This will provide a better understanding of the technology, materials’ characteristics and performance over time to support future uses and to understand its wider application within the construction industry.
The design of the geometric shape of the product uses curves instead of straight lines. Without the need for steel reinforcement, this represents a significant and sustainable saving in costs and material, according to National Highways.
Joanna White, roads development director at National Highways, said: “We’re committed to exploring sustainable and innovative ways of constructing and maintaining our roads.”
Bhavika Ramrakhyani, head of materials at Costain, added: “This provides a step-change in the construction industry that there is no ‘one size fits all’, but different solutions are needed to combat climate change and increase productivity in parallel.”
This article was first published on BIMplus